
Wearable medical devices have liberated patients across the world, allowing users to manage many conditions without the need for many visits to medical centres. However, creating such a device requires all stages of design, manufacture and end-of-life disposal to be carefully co-ordinated to avoid costly design impacts, operational failure and risk to the end-user. Dr Del R Lawson, lead of new product development and commercialization in 3M’s Medical Solutions Division, explains the process.
Wearable medical devices have been game-changers in enabling highly tailored treatment options and ways for patients to monitor their health and chronic illness themselves. Wearables enable patients to access health data that allows them to make health decisions from the comfort of their daily life.
Designing a wearable medical device that functions as intended and meets patient needs is no easy feat. Much forethought, time and effort are required. To improve people’s quality of life and eliminate stressors, wearable medical devices need to be life-proofed, comfortable, easy to use, long-lasting in power and personalised.
Thoughtful material selection is critical in a medical device’s success. It is important to consider material selection and potential materials suppliers at the outset of the design process. If too much time passes and design decisions are finalised, even small decisions made early in the design process can have costly impacts.
All elements under consideration in the design process of wearable devices
There are a number of considerations to keep in mind when attempting to build successful medical devices:
Using incompatible materials: not all materials are compatible with one another and with every substrate. Incompatible material combinations can result in myriad consequences, ranging from design issues to manufacturing problems.
Treating adhesive selection as a trivial exercise: adhesive influences overall functionality and accuracy, playing an important role in the device’s total system. If adhesive selection isn’t thought about early in the design process and optimised for the application, it can result in manufacturing issues, device malfunctions and harm to the user.
Evaluate power sources early on: when managing a chronic illness, losing power on a wearable is problematic and potentially life-threatening. It could mean going without data needed to make critical health decisions. Deciding to make a device rechargeable or battery-operated is not one to make lightly.
Creating a cumbersome or unintuitive application process: research can play a part in identifying design nuances and other insights to create a simpler application process for your end user. A process with fewer steps can help people get the application right the first time.
Proper disposal of a device is a safety and environmental concern: when designing devices, it’s important to map its entire lifespan, from inception to disposal. Its materials, components and intended function all influence your disposal options.
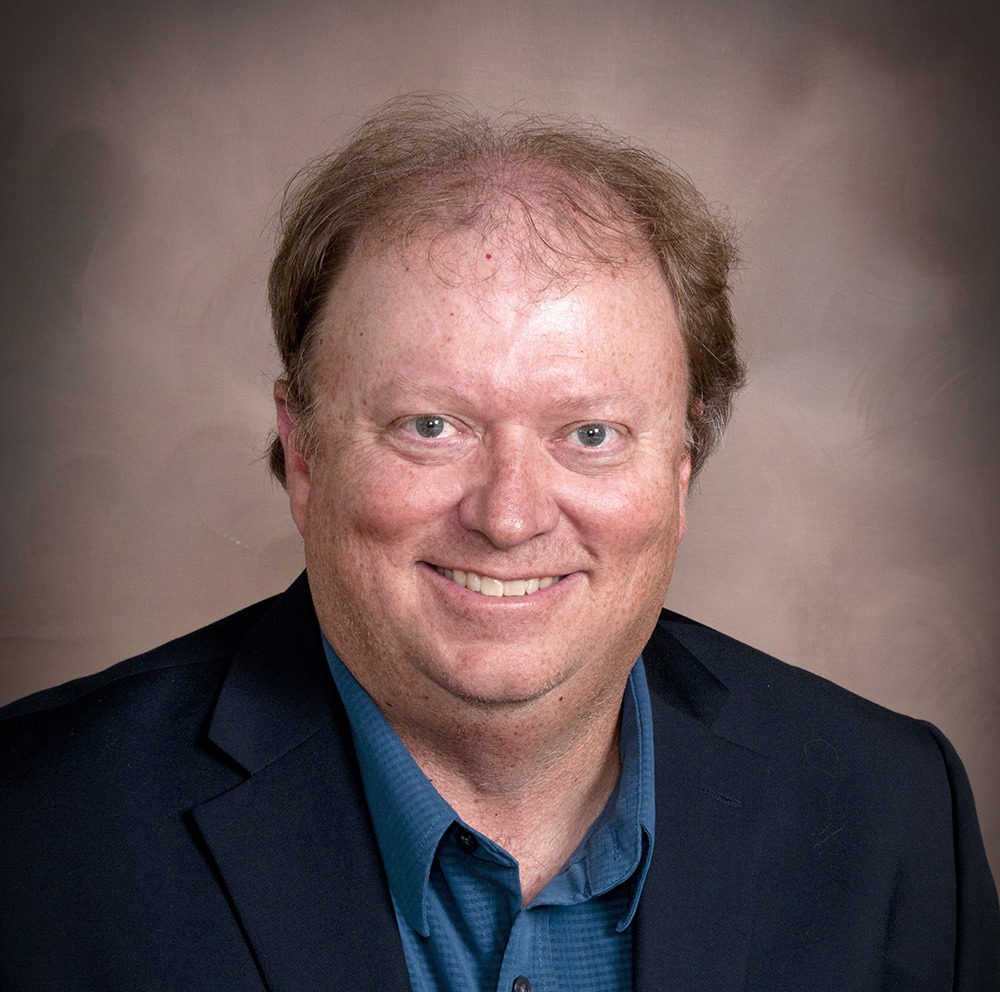
Issues with unexpected interference: wearable devices incorporating electronics are more complicated to create than ones that do not. Ensuring the device is adequately protected against interferences to keep the device and its user safe should not be an afterthought.
Choosing incompatible sterilisation methods: there are three main types of sterilisation used with wearable devices – ethylene oxide gas, e-beam and gamma radiation. For devices that need to be sterilised, the entire construction should be designed to withstand the method.
Running accelerated-ageing testing at too high of a temperature: materials for wearable devices will be used on people and likely won’t need to withstand the same temperature extremes. Raising the temperature above the recommended 50°C (120°F) to accelerate the ageing process may yield inaccurate results and compromise the study.
Failing to foresee manufacturing process implications: Materials need to withstand the speed and friction of the desired manufacturing process. Thinking through how a device will be manufactured early in the process can help avoid redesigns, delays, cost overruns and issues during the scale-up process.
There is a lot to think about when designing and bringing to market the next generation of wearable medical devices intended to improve people’s lives. To ensure wearable medical devices are ready to go to market, they need to be flawlessly manufactured, sufficiently tested and – in some cases – sterilised, without issue and to standard.
About the author