Nanoscribe's new material, IP-n162, features a high refractive index coupled with a low Abbe number, making it 'attractive' for 3D-printed micro-optics
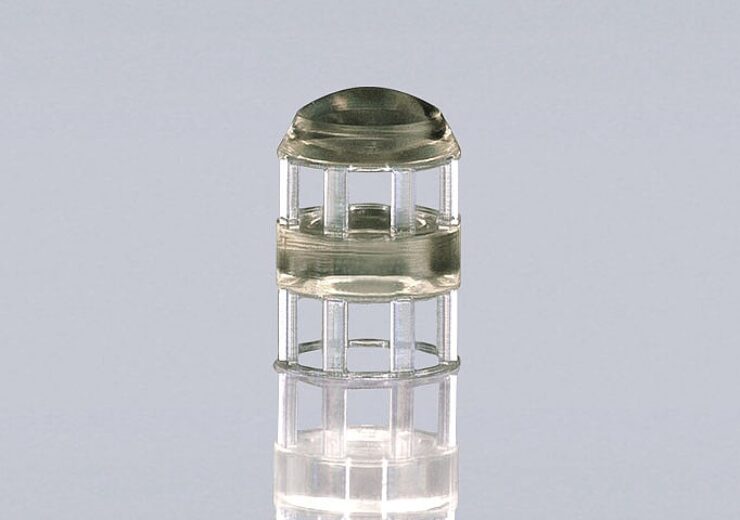
A compound lens system printed by Nanoscribe with its new additive manufacturing material photoresist IP-n162 (Credit: Nanoscribe)
A novel 3D printing material from Nanoscribe opens up “new possibilities” when designing lenses for micro-optic devices.
German nanotechnology firm Nanoscribe has introduced its photoresist IP-n162 – a high-index polymer specifically developed for the additive manufacturing of innovative micro-optical designs.
IP-n162 has a high refractive index, which means light that passes through it refracts or ‘bends’ more.
This makes it “attractive” when 3D printing high-precision microlenses and freeform micro-optics with a high degree of shape accuracy, and surface quality, according to Nanoscribe.
IP-n162 also has a low Abbe number of 25, meaning chromatic aberration – the failure of a lens to focus all colours to the same point – can be corrected due to a higher level of dispersion.
Its low absorption of infrared light makes the new printing material particularly suitable for 3D-printed infrared micro-optic applications – including optical communication systems, quantum technology and photonic packaging.
Simon Thiele, project participant in the BMBF-funded project PRINTOPTICS, and CTO of a spin-off company with the same name, said: “A photoresist with a high refractive index, such as IP-n162, opens up new possibilities in the design of more powerful, thinner and less curved lenses, which in turn can be made more compact, faster and cheaper.
“An innovative design that I was able to print with IP-n162 was a complex optical system. It consists of two lenses with complete free-form surfaces in order to obtain a truly distortion-free image.
“A special feature is the integrated diffractive lens with fine staircase structures at the top of the lens to correct colour errors – the high refractive index of IP-n162 helps to reduce these steps and thus to reduce stray light.”
What are the benefits of using a high-index polymer material in 3D printing?
High-index polymers support the functions of a large number of innovative technologies.
For example, in optoelectronic applications – which are electronics that source, detect or control light – they allow the optical and visual properties of displays, cameras and optical projectors to be optimized.
Nanoscribe claims the availability of these materials in 3D microfabrication – manufacturing miniature items and structures using 3D printing – can lead to a new class of innovative, compact and complex micro-optics being established.
Compared to the ones used in more traditional optics today, these materials are much smaller and, according to Nanoscribe, will shape miniaturised imaging systems, endomicroscopy and sensors for applications in augmented reality (AR) and virtual reality (VR).
And, as a high-index polymer with a low Abbe number, IP-n162’s optical properties are “close” to optical polymers like polycarbonate or polyester – which are typically used in injection moulding processes.
Nanoscribe states that these properties are also “advantageous” in the prototyping of micro-optics, meaning more expensive iterations with diamond-milled injection moulding tools are “a thing of the past”.