
As devices get ever smaller in the pursuit of extra convenience, cost-savings and patient safety, micro moulding is increasingly coming into its own within the medtech sector. Jamie Bell speaks to Accumold’s Aaron Johnson about the pros, the cons, and the potential of this manufacturing method for companies in the medical industry.
On an average day — that is, an average day as we knew it before the Covid-19 pandemic — you would most likely encounter numerous objects that were made using injection moulding.
The bumpers of cars driving past as you walk down the street were made using injection moulding — as were the dashboard, the cup holders, and many of the controls and switches found inside these vehicles.
The cap from the bottle of water you buy on the way to work, the plastic container you eat your pre-prepared lunch from, and even the toys found in Happy Meals at the McDonald’s you pass were all made using injection moulding.
But what about the objects you don’t see?
Many electronic products including mobile phones, smartwatches and TV remotes all contain a great number of tiny, but highly specialised parts that are crucial in giving these technologies the multifunctionality to meet the demands of modern life.
This is where the process of micro moulding — a type of injection moulding used to make very small plastic objects — comes into play.
Micro moulding technology enables this “miniaturisation” of objects and individual components to be completed extremely precisely, and this precision is perhaps more important in healthcare, and in the manufacturing of medical devices, than anywhere else.
One of the leading providers of micro moulding in the world today is US firm Accumold, and Aaron Johnson, the company’s vice president of marketing and customer strategy, believes micro moulding has an ever-more crucial role to play within the medtech industry.
“The demand to shrink devices is putting pressure on form factors to accomplish their goals, and sometimes it fights against what traditional injection moulding would say,” he says.
“It really takes experience in micro moulding to understand how it can be done successfully and where those limits can be pushed.
“What we’ve been seeing over the past 30 years, but particularly over the past decade, is a really fast rise in interest in microtechnology — especially in medical devices.
“And we don’t really see that trend slowing because of the value of miniaturisation for surgical devices, patient diagnostics, and point-of-care wearable technology.
“There are so many advantages to these being small, discreet and less invasive, and miniaturisation is certainly one of the major keys to that.”
The Accumold approach to micro moulding
Accumold began life more than three decades ago, and first started making small, injection moulded components in 1985 using its Micro-Mold platform.
Today, the Iowa-based firm produces millions of these small parts for companies in several markets including micro electronics, automotive electronics, fibre optics, the medical sector, and emerging technologies.
As with the established production method of regular injection moulding, micro moulding involves injecting a molten material into a mould to create a 3D shape.
It can also be carried out with a range of materials including metal, glass and plastic — although the vast majority of Accumold’s work involves specific types of plastics called engineering-grade resins, which are stronger, more durable and more resistant to high temperatures than standard “commodity plastics”.
However, this is about more than just carrying out regular injection moulding on a smaller scale.
According to Johnson, there are three nuanced processes that micro moulding can refer to, and many of the projects Accumold undertakes will involve a combination of all three.
The first and most obvious of these is micro moulding in the traditional sense — the process of making very small, very precise components that are only a handful of millimetres, or even micrometres/microns (one-thousandth of a millimetre), in size.
The second way Accumold defines micro moulding is with “micro features” that make up or appear on a larger object.
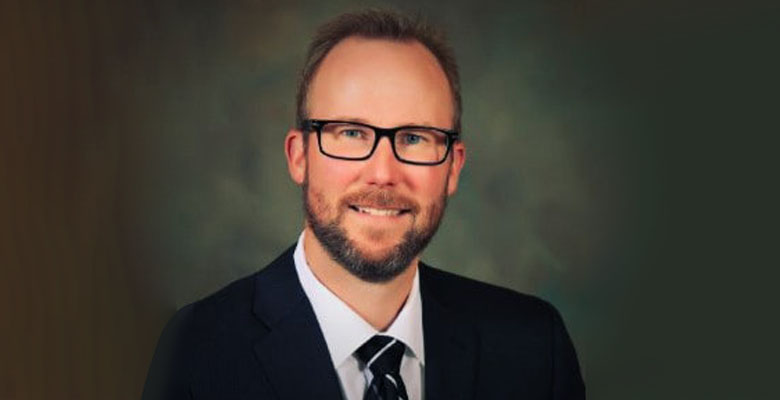
“Let’s say you have a slightly larger part, but there are microfluidic channels on it — one of the larger parts we’ve moulded is a cartridge for a medical diagnostics application,” Johnson says.
“That’s about four or five centimetres in length but it has little microfluidic, hundred micron-wide channels for fluid management.
“So, here you have a big part, but it has micro features to it that may be a little bit beyond a traditional moulder’s experience.”
The third and final way Accumold defines micro moulding is with “micro tolerance”, which essentially refers to the room for error, and the accuracy and exactness to which an object’s specifications are moulded.
“If we say that something is going to be one millimetre long, the tolerance could be plus or minus five microns, and success will be if it’s less than five microns shorter or five microns taller than one millimetre,” Johnson says.
“When I first started at Accumold, I remember sitting in an office where people were talking about the difference between five and ten microns like you could drive a truck through it — and they say the average human hair is about 90 microns in diameter.
“So, we’re talking fractions of a fraction in terms of accuracy levels for plastics, and it’s quite extraordinary and difficult to achieve.”
The miniaturisation of medical devices
Many medical devices and technologies used in patient care are already very small — most notably those that are invasive, and need to be scaled down enough to fit inside parts of a person’s anatomy without causing damage, or further health complications.
Intravenous lines and catheters need to be able to fit within the diameter of a human blood vessel. Traction pins, used to stabilise broken bones while they heal, have to be fine enough to be inserted through the skin without leaving major scarring, and cardiac pacemakers need to fit into a relatively concise area beside the heart to perform their intended function.
But one of the key ways micro moulding can improve this use of microtechnology in the healthcare industry is by making it possible to pack even more into these tools without making them any bigger.
“When it comes to a catheter, for example, your veins aren’t going to get any bigger just because you want to put more inside it, so we have to figure out how to make things smaller in order to do this,” Johnson says.
“And here, these micro tolerances are so tight. There’s just no room left, there’s no extra wiggle room to put multiple things into, let’s say, a catheter, and it’s got to fit right so that when it’s deployed, it functions correctly.
“That’s one of many reasons why quality is paramount in the type of work that we do.”
Johnson says Accumold has worked on several projects involving transcatheter, endoscopic tools, including cameras used to look inside a patient’s body, and even drug delivery devices.
He also cites one particular example of the former — a tiny, reflective mirror that rotates to take internal images of the human heart.
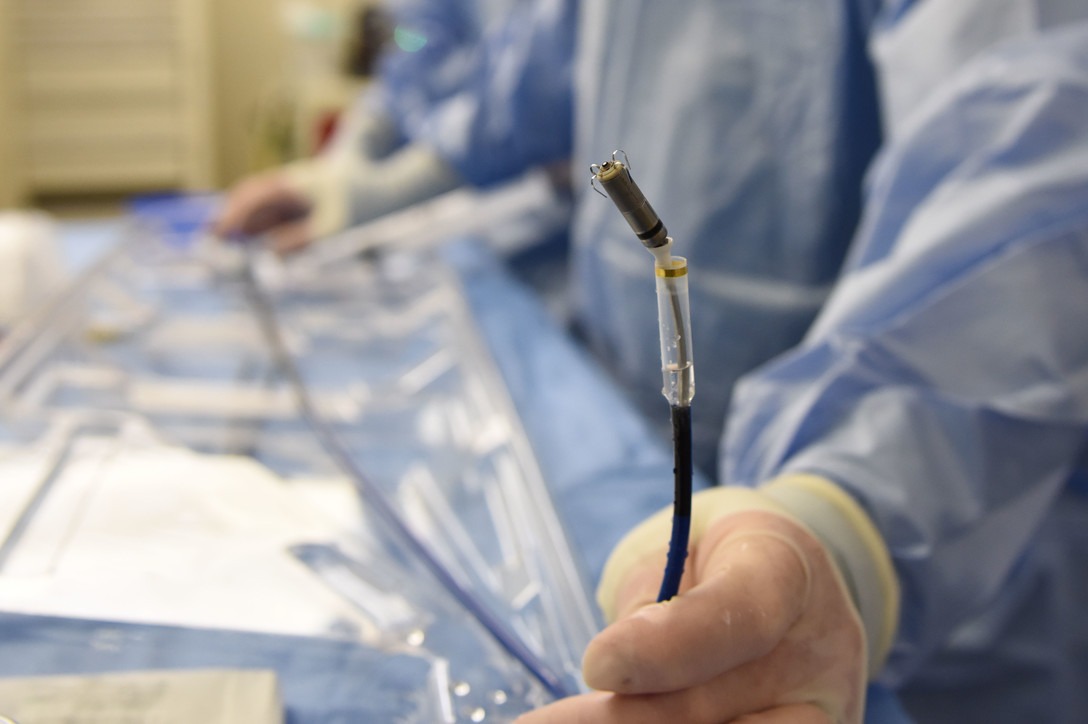
By capturing very precise images, that device has allowed doctors to target a more specific, exact area of the heart — rather than cauterising a whole section of it — which removed some potential side effects, and decreased recovery times for affected patients.
On top of the miniaturisation of medical devices, Johnson also believes the convergence between this market and consumer electronics has provided a “whole new world of potential” for micro moulding.
“A hearing aid used to just amplify sound. Today, they actually listen to that sound, they process it, they decide what to tell you, and they transcode it into digital and give you a stereo spatial sound that was never really achievable before.
“Then, in addition, some hearing aid companies have added Bluetooth so you have a discreet connection to your phone.
“Others have added heart rate monitors, or step counters, and now you have this extra capability — because why not? You already have that device there on your body, and you might as well take advantage of that.”
To fit all of these different capabilities into a device no bigger than a couple of centimetres in diameter, micro moulding can play a crucial role by allowing manufacturers to make the necessary sensors and technologies smaller than ever before.
“There’s certainly a big potential, and I think we’ve only scratched the surface when it comes to where miniaturisation can go for medical devices, and its value to both doctors and patients,” Johnson adds.
Challenges in micro moulding
Micro moulding may have its advantages in medical device manufacturing, but there are limitations to what it can accomplish in this sphere as well.
One of these is the logistical challenge around the materials that are used — which is something that comes with just about any production method out there.
As Johnson says, the relationship between material selection and feature performance is “very profound” in micro moulding, meaning a certain material may be suitable for creating the exact geometry of a device, but doesn’t have other qualities necessary for it to function properly.
“As companies are looking for smaller and smaller things, the material has to be able to handle that — for example, microelectronics requires heat control, and materials that can withstand high temperatures in the manufacturing process, or operational heat,” Johnson adds.
“It’s plastic, and if you get it hot enough, it melts. There are materials that have higher heat resistance than others, but matching high heat resistance to, let’s say, optical quality of components, can also be a struggle.”
In the medical devices sector specifically, the age-old theme of the industry often being adverse to substantial change is also present, and is something of a cultural barrier in micro moulding at times.
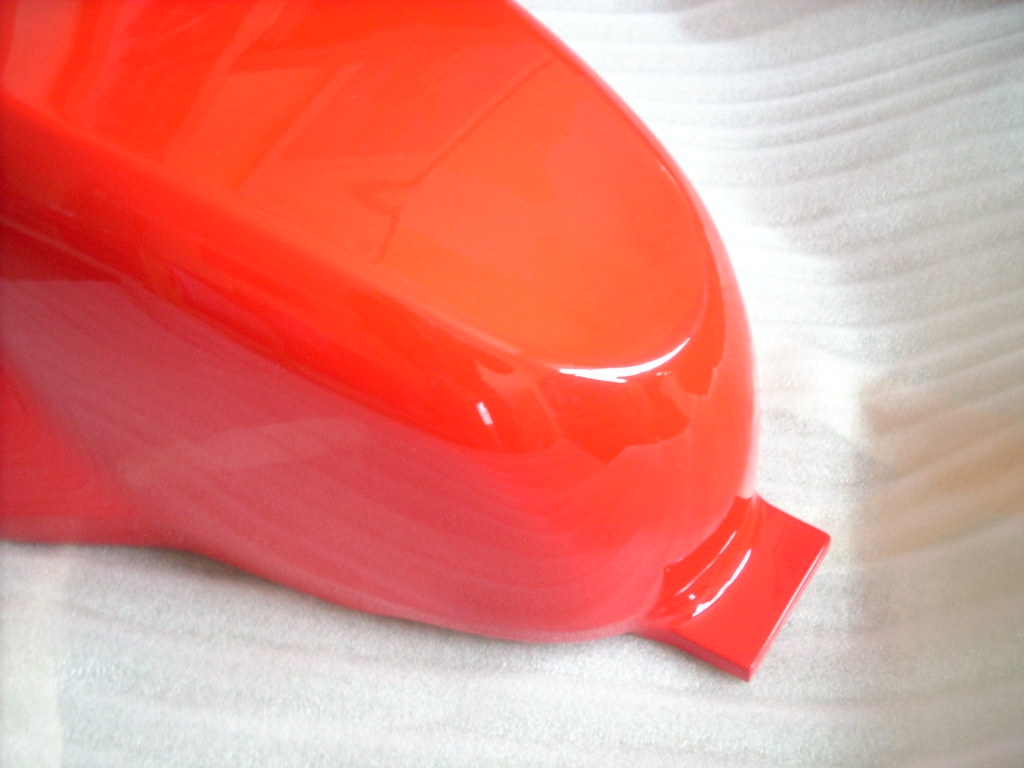
As Johnson notes, once a device has been built, it goes through a “tremendous qualification and regulatory process”, meaning it has to be made in the same way, and to the exact same specifications, as any subsequent parts.
While stringent regulation is totally necessary, it can potentially hinder innovation and the implementation of newer technologies, according to Johnson.
Because of this, he emphasises the need for companies to ensure micro moulding is not only capable of making their device, but also provides the right scalability and sustainability by having a supply chain in place that can cope with demand for a device that’s on the market for a decade, or more.
However, a lot of hurdles in the work Accumold does are simply part of its role as an innovator, and stem from the creativity of companies looking to micro mould a new device.
“Everything that we’ve ever made has never been made before — it’s all bespoke, and we encourage our customers to come to us with a crazy napkin sketch, and to tell us what they really need to make their product successful, so that we can start from there,” Johnson says.
“And sometimes you can push those limits, and sometimes you can’t, so there’s always that challenge of finding out whether a part is actually mouldable.”
How can companies utilise the full potential of micro moulding?
Micro moulding may have been around for several decades now, but as a very specialised, niche manufacturing process, many companies may not be as familiar with it as they are with regular injection moulding, or even newer production methods like additive manufacturing.
One key piece of advice, Johnson says he would give to a company looking into micro moulding as a manufacturing method for its device, ties in with the aforementioned challenge of innovation.
“We encourage starting with what you need, and starting with your ideal in mind, because you might just find that ideal is achievable,” he says.
“Every situation is different at the micro level, and that leaves a lot of opportunity on the table.
“We’re interested in helping our customers push those limits where they can — sometimes we can’t, but let’s start with that, and then work our way towards something else if what they’re after is not really manufacturable.”
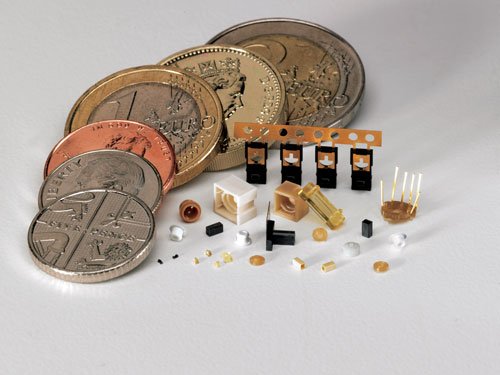
What’s just as important as identifying what you want to accomplish first and then assessing the available options within micro moulding, in Johnson’s view, is not allowing traditions to stifle your innovation.
“Sometimes it’s just easier to go down a certain path because you already know a supplier, or maybe the contract manufacturer you’re using doesn’t have micro moulding, and they’re not necessarily going to drive you towards something that they can’t do,” he adds.
“But you need to think about it in terms where you’re seeking it out — and this goes for any specialised technology that might bring value to your organisation, not just micro moulding.
“It’s worth digging into and seeing how it might be implemented in your ecosystems, and you might just be able to revolutionise what you’re doing because you’re stepping outside of the normal path your organisation is used to in terms of product design.
“The miniaturisation trend is not going away, and therefore I think the advantages and value of micro moulding will continue to be added to people’s thought processes as they’re designing next-generation products.”