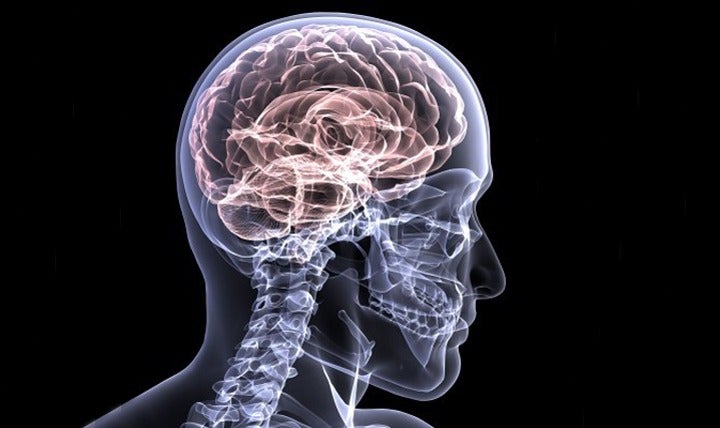
A robot that can listen to how human brain neurons communicate with each other has been created – and it even has its own Twitter account to record interactions.
Known as the patcherBot, it listens to individual electrical properties within brain cells and measures the power and time it takes for them to travel.
It has been dubbed the “world’s first social neuroscience robot” and helps scientists by automating the popular patch clamp technique, which until now has been used to understand how the brain works.
Craig Forest, a researcher in the Petit Institute for Bioengineering and Bioscience at the Georgia Institute of Technology in the US, and his team spent six years developing the technology and made it commercially available this month.
I got a whole-cell all by myself! It’s 11:09:07 AM and I’m not even tired yet. pic.twitter.com/rR2MYy7c5B
— patcherBot (@patcherbot) December 13, 2017
He told Compelo: “There is no other way to perform patch clamping in a repeated and sequential fashion without the patcherBot, whether it’s automated or manual.
“Most researchers who perform this technique sit in front of a telephone booth-sized apparatus for more than eight hours per day, performing dexterous and tedious tasks to patch clamp cells.
“But the patcherBot fully automates the process, removing the need for a human entirely.”
What is the patch clamp technique?
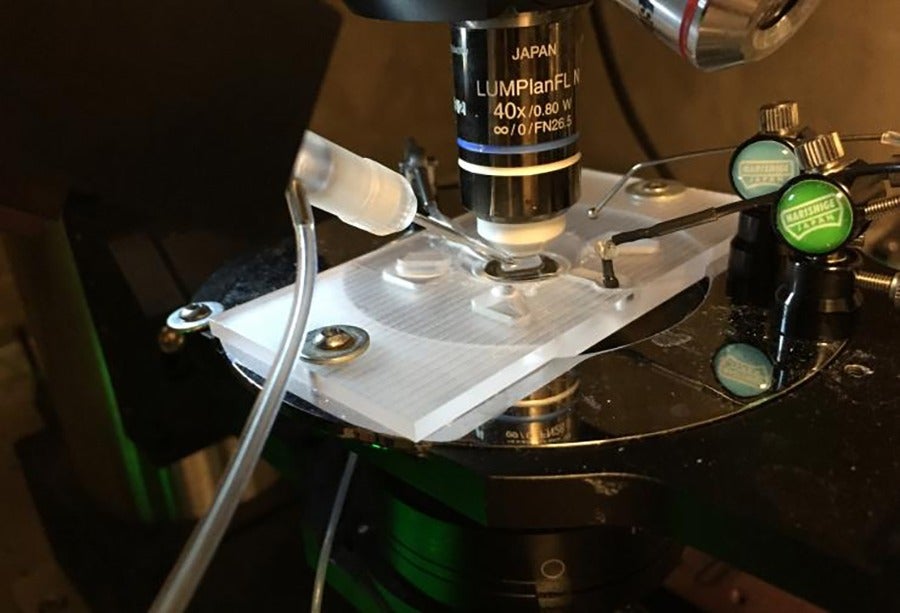
The patch clamp method is known as the gold standard for measuring the electrical properties of individual brain cells.
It’s a useful process that investigates the electrical activity of single ion channels, which control the movement of charge into and out of the neuron cell membranes.
It involves sending an electrical connection to the cell via a micropipette to pick up its properties and separating a “patch” of membrane containing ion channels.
Researchers can then “clamp” the electrical properties of the membrane and use them for research and analysis in neuroscience.
This allows researchers to gather information by “eavesdropping on the furtive chattering of neurons in the ongoing effort to unlock the brain’s secrets”.
The patcherBot doesn’t just observe how neurons communicate with each other – it also cleans medical equipment
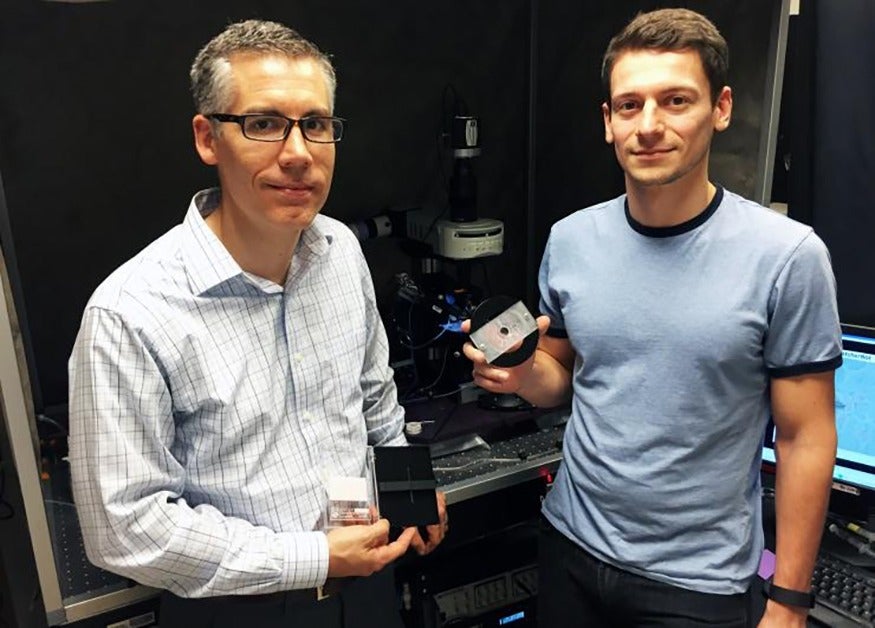
The patchRobot developed in the Georgia Tech lab provides image guidance to target the same neurons.
One of Mr Forest’s researchers, university graduate Ilya Kolb, also discovered a solution using the cleaning detergent Alconox to sanitise the pipettes.
He reprogrammed the software operating the patcherBot to add cleaning and rinsing steps between each recording.
The entire cleaning process takes about a minute – faster than a trained human operator, who doesn’t need to be present as the robot works autonomously.
It means they micropipettes don’t need to be thrown away between recordings after a single use, which has often previously been the case.
Mr Forest said: “Discovering the method by which patch clamp pipettes could be made reusable, quickly and easily took years of effort.”
What next for the patcherBot?
The patcherBot has already gained some public attention due to its Twitter account, in which the robot automatically shares its activities.
This involves publishing graphs that illustrate the time it takes for neurons to communicate with each other and the voltage power of the electrical current between them.
Helping humanity solve the brain one whole-cell patch-clamp recording at a time. 3:18:52 PM. #slice pic.twitter.com/ergnViNaQz
— patcherBot (@patcherbot) December 15, 2017
Mr Forest believes there will be plenty of uses for the robot.
He added: “A few of the reasons why many companies and labs perform large-scale patch clamping studies could be for drug screening, genetic variant screening, cell type screening and many more cases.
“We envision our robot to evolve until it is a bench-top tool in every biology lab, from high schools to huge pharmaceutical companies.”
It is now being made commercially available to researchers after patcherBot signed a licensing agreement with Sensapex, an electrophysiology device company based in Finland.
The first patcherBot has already been ordered by Janelia Research Campus, part of the Howard Hughes Medical Institute in Maryland, US, and it will receive the robot in April 2019.