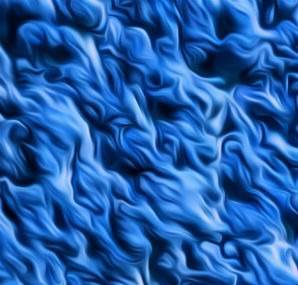
In our aging society, healthcare is becoming ever more important, and is accompanied by an increased need for care at home as well as for technical assistance. However, with that comes extra cost pressure, as more services at lower cost are expected. The solution is technical tools that make it possible to ensure the best care and support with a minimal amount of personnel; new technologies are developed every day – from mobile monitoring of vital parameters, using mobile diagnostics with simultaneous automatic dosing of drugs, to nursing robots.
Microtechnology can play a crucial role in meeting healthcare goals. For example, sensors must be developed that transmit data periodically to diagnostic detectors, and must be worn on the body of the patient. These so-called ‘wearables’ can be in the form of an in-ear sensor for measuring the pulse and oxygen/carbon dioxide content of the blood, as developed by German firm CiS, or fixed in a belt with integrated electronics.
‘Smart textiles’, too, have a part to play, incorporating electronic components, such as displays in the clothing as memory aids for people with dementia, which have been developed by Fraunhofer IZM. Here, the concepts have to allow for washing, stretching and adaptation to the patient’s body without destroying the added electronic functions.
All these mobile units must possess a self-sufficient energy supply. With ‘energy harvesting’, for example, energy is pulled from the body heat or movement of the patient so that no external power source or battery is necessary. Miniaturised transmitting and receiving units are also important.
In all these areas, the first products are on the market, although major R&D is still required.
Diagnostics
One of the most important advances in recent years has been the ability to transfer complex analytical or diagnostic processes into a single microfluidics device. These devices are the size of a microscope slide at most and contain channel systems for transporting liquids and gases, as well as for mixing, performing reactions and separating. The channel dimensions are in the range of several 100µm for devices that produce substances such as pharmaceutical products and 10-40µm for analytical devices, the so-called ‘lab-on-a-chip’.
The first microfluidic components were developed for chemical applications. The unique advantages of these ‘microreactors’ are enhanced heat transfer due to the large surface area-to-volume ratio, which allows a precise temperature control of reactions. The length scale of diffusion processes is comparable to that of the microchannels or even shorter, while an efficient mixing of reactants can be achieved during very short times, typically milliseconds. In other words, with microreactors the chemistry is much more efficient, faster and is perfectly controlled. It allows the handling of small amounts of substances, but, by parallelisation, it is also possible to produce large quantities of a substance.
Another advantage is decentralised, local production; for example, in the production of radiopharmaceuticals at a hospital. This is necessary because these substances have a half-life of only a few minutes and cannot be transported from a factory over days. Microreactors are able to produce the exact amount of the pharmaceutical compound needed for one patient, in a short time, on-site, in a good quality.
Due to being able to handle small amounts of liquids, microfluidic devices can be used for the treatment of patients at the point of care. The term ‘point-of-care testing’ (POCT) applies to processes and devices used either directly on the patient or a very short distance from them, and allows for diagnosis outside the traditional central laboratory of a hospital and requires no special infrastructure to operate.
Mobile diagnostics makes different demands on the equipment and methods compared with diagnosis in a central laboratory. First, the device must be small. It must also be simple and easy to use even by untrained personnel. All individual steps of a test method must be integrated too – from the sample application, the separation processes and chemical reactions, to the evaluation of results and the derivation of therapeutic consequences. All of this can be provided by microfluidic components. They are robust, easy to manufacture, and easy to handle. The behaviour of the liquids is controlled mainly by the design of the channel system, so the results are therefore independent of the user and very reproducible.
Manufacturing
Different materials are available for microfluidic structures. Glass has the big advantage of being chemically inert and biocompatible. It can be micro-structured by photolithographic and wet-etching processes comparable to those of electronic chip production, while laser processes have been reported to give good results. A special glass material called Foturan and produced by Schott of Germany is used by a company called Invenios to manufacture glass chips for chemical production as well as for DNA analysis. Using this material, Invenios is able to demonstrate that a price of several euros per chip is possible for large-volume production. This allows glass chips to become disposable, which is required for POCT.
In general, however, plastic materials are favoured for cost reasons. There are different processes available that all lead to very accurate microfluidic structures at very low production costs of just a few cents a chip at high volume.
UK-based firm Microsystems has shown how to organise mass production of diagnostic chips using injection moulding. Its lab-on-a-chip device consists of two plates:
- In the base plate, the 300µm microchannels and chambers with static mixing features are moulded, and so is an optical lens. The function of this lens is to permit the automatic checking of fluidic reaction results – for example, with the use of a camera.
- The top part is characterised by three Luer cones. Two of these connections are used to feed liquids into the system: one sample liquid and one reagent. The flow rate is controlled via the third Luer cone by applying a vacuum in order to reinforce the capillary effect.
After moulding, the two parts are tested for dimensional stability, absence of flashes and optical purity. Then the two parts are overmoulded in another injection-moulding machine by TPE material to form a handle element. The lab-on-a-chip is now ready for use and can be inserted into a hand-carried measuring instrument; for example, for the execution of a blood or urine test for drugs.
German business CDA also uses injection moulding for its microfluidic products. Using its knowledge of compact disc production, it developed new applications with the University of Helsinki, such as multi-array microchannel discs for mass spectrometrical analytics.
The Institute for Micro and Information Technology (HSG-IMIT) in Germany also uses the shape of a disc for its microfluidics. The surface of the microchannels can be functionalised and the chambers prefilled with the required reagents or solvents. The disc is an analytical machine able to move the liquids within the channel system by centrifugal forces – so, without any additional pumps, fluids can be moved to all the necessary parts of the disc. This small machine can be used anywhere, is easily operated by non-professionals, and has automated diagnosis and evaluation software. Such a system could be used for immunoassays as well as for DNA analysis.
Additional functions
In many cases, the microfluidic structure itself is not enough, and additional functions such as pumps and sensors have to be included.
Micro pumps can also be manufactured out of polymer materials in a mass production process such as injection moulding.
Bartels Mikrotechnik from Dortmund is producing a piezoelectric membrane pump out of polypropylene that’s the size of a thumbnail. Possible applications for the pumps are delivery systems used in infusion therapies, liquid drug-dispensing nebulisers, or the analysis of breathing gas. These areas require high flow accuracy or a continuous dosing of liquids or gases, which the pump can fulfil. It ensures reliable fluid supply and provides an ideal solution for portable and stationary devices.
As it is necessary to detect the functions of the microfluidic device and measure the medical parameters, sensors are necessary. These are provided by the likes of Swiss company Sensirion. Having a history of semi-conductor fabrication, Sensirion is able to provide, for example, a disposable liquid flow sensor with a fully calibrated and linearised signal output for flows of between 0.1nl/min and 5ml/min. Inert medical-grade wetted materials, such as glass, ceramics, PEEK or stainless steel ensure sterile operation with no contamination of the fluids.
Summary
Microfluidics is very important for mobile diagnostic devices. The technologies to produce such devices are available, as are the materials to make the devices biocompatible and cost-effective. The main advantage is that the design of the device fixes the function. As a result, the technology is very easy to use, even for untrained users such as the patients themselves. However, this advantage also means that medical doctors and material/microtechnology specialists have to work very closely together to develop the necessary chip design for every single application.
At the moment, diagnostic devices in particular are on the market, but more and more therapy devices are being developed, such as sensors for measuring blood-sugar level that are connected to an insulin pump to give the exact necessary dose of insulin into the body.
For this, it is important that microfluidic structures are supported by other tools such as pumps, sensors and energy supplies. All together, this makes mobile diagnostics a powerful tool for our healthcare system for the following reasons:
- the costs in the healthcare system can be reduced
- patients can live in their normal environment with controlled vital parameters
- laboratories will need less space for diagnostic equipment
- results of measurements are available much sooner and will lead to fast and more effective treatment of diseases.
All the products mentioned will be shown on the IVAM joint pavilion at the COMPAMED exhibition, which takes place in Dusseldorf, Germany, 12-14 November 2014.