On June 18th Oliver Healthcare Packaging is celebrating the grand opening of our new 1450 square meter cleanroom. This investment in Venray is pivotal to enable our medical device and pharmaceutical customers to provide uninterrupted service to patients in Europe and globally. With this new cleanroom we triple our manufacturing footprint and further employment opportunities in a critically important market, in Limburg.
This investment in Venray is pivotal to enable our medical device and pharmaceutical customers to provide uninterrupted service to patients in Europe and globally. With this new cleanroom we triple our manufacturing footprint and further employment opportunities in a critically important market, in Limburg.
Over the last ten years, Oliver HCP has made significant investments in the EMEA region. The last four years, the market dynamics have evolved such that there is a much greater focus in our market to source and produce locally. We know how important it is to produce packaging in region, for region, to de-risk the supply chain, serve the customer effectively and more importantly be a more environmentally conscious business.
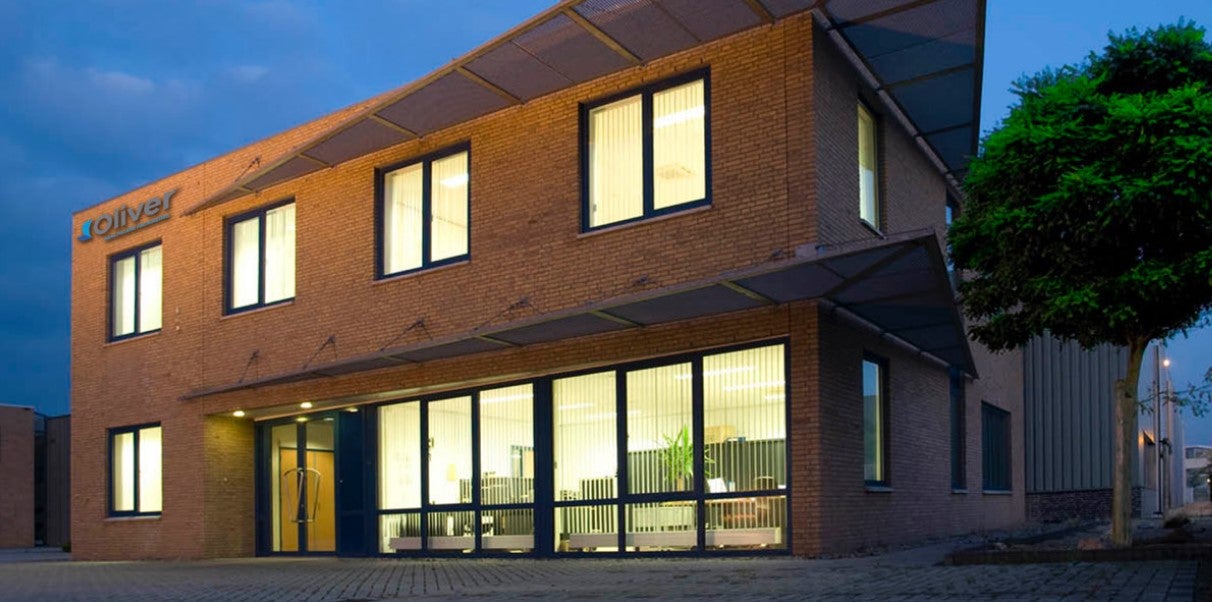
Oliver Healthcare Packaging is a converter and supplier of Healthcare Packaging. We produce packaging that protects medical devices and pharmaceutical products. Our packaging is developed and designed to protect the sterile barrier around these medical devices. Examples of such devices are heart valves, knee implants, catheters or syringes filled with vaccines. These products go into the human body, sometimes even to stay there, so you want them to be sterile. Our packaging protects these products throughout the sterilisation, shipment and storage processes until they are opened in an operating theater and that is the reason they are produced in a cleanroom.
It is not just packaging, it is packaging that helps save lives. It is extremely important that this is produced the right way and that we continue to invest to be best in class in our industry. This is a great milestone for us and our Venray community and therefore request you to join us on 28 June 2023.
For more information please contact: Anneke Willems (awillems@oliverhcp.com | 0478 517564).