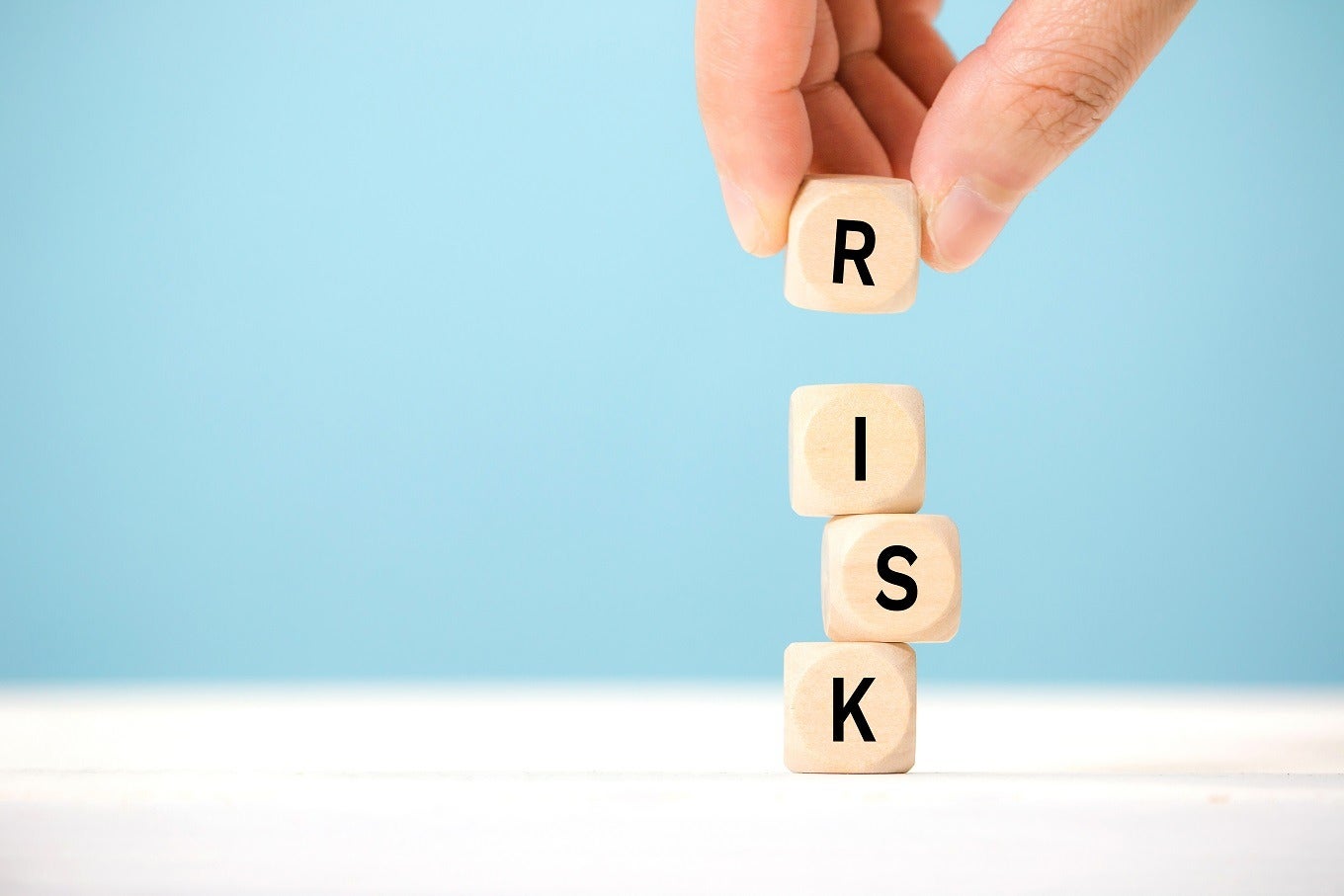
Supply chain planning is not, by any means, a brand new concept for medical device manufacturers – it’s something they’ve been doing for decades to optimise their production processes and overall business setups. However, the idea of scenario planning, and mitigating the resulting risks if certain scenarios do materialise, has taken on fresh importance during the global Covid-19 pandemic. Jamie Bell speaks to Tekni-Plex’s Brian Clarke to find out what OEMs can do to prepare for similar crises in the future.
While there are undoubtedly many lessons society will learn from the Covid-19 pandemic, one thing remains fairly murky as we look towards the future – how do you plan for the unexpected?
Numerous companies that were in a strong position heading into 2020 suffered heavily throughout the year.
The most extreme examples have been seen in the travel and retail sectors – with the likes of Flybe, Virgin Australia, J. C. Penney and the Arcadia Group all filing for bankruptcy within the past 12 months.
Due to the central role the industry continues to play in treating and slowing the spread of the viral infection, companies in the medical device sector have generally managed to keep their heads above water where those in other areas have not – although this period has not been without its roadblocks.
Tekni-Plex, a Pennsylvania-based company supplying materials and components to many medical device OEMS (original equipment manufacturers), had to negotiate one of these hurdles early last year.
The company worked with a leading American medtech firm to urgently change the design of a tubing component for intravenous infusion pumps being used to treat severely ill coronavirus patients in hospitals – doing so in a matter of weeks.
However, while both parties moved swiftly and effectively to remedy this tricky situation, Brian Clarke – Tekni-Plex’s senior business development manager for EMEA and SE Asia – believes the focus moving forward should be on preparing for these unprecedented situations more effectively beforehand.
“These uncommon events are becoming incredibly common – if it’s not Covid-19, it’s a typhoon, or wildfires in California, or geopolitical events that cause issues with supply chains,” he says.
“In the future, medical device companies will really have to do better scenario planning and risk analysis on their supply chains, to make sure they account for these eventualities from the outset.
“And, it’s ultimately easier to do this from the outset rather than rebuilding the plane while you’re in flight, which has happened a lot during the pandemic.
“Scrambling around reactively, and trying to requalify medical devices and products in the middle of a crisis is a lot more expensive, a lot more stressful, and could lead to stockouts and other issues that impact your customers.”
Existing medical device supply chain challenges
Certain elements of the medical device supply chain are challenging to negotiate and, as Clarke puts it, “finely balanced” even without taking global pandemics and natural disasters into account.
The primary factor here is the strict regulation the industry is subjected to.
Production and manufacturing processes must pass ISO (International Organization for Standardization) guidelines, while commercialising medical device products requires clearance through the FDA in the US, approval from the MHRA in the UK, or a CE marking in the EU – with the latter becoming even more onerous this year due to the introduction of the new MDR.
For OEMs, this makes choosing the quote-on-quote best material – and, by proxy, the most appropriate supplier – somewhat difficult, because affordability and practicality need to be accounted for alongside choosing a material that will function effectively in line with the relevant regulations.
And, as is the case across the entire medical device supply chain, not to mention the healthcare industry in general, patient safety should always be considered of paramount importance when selecting these components too.
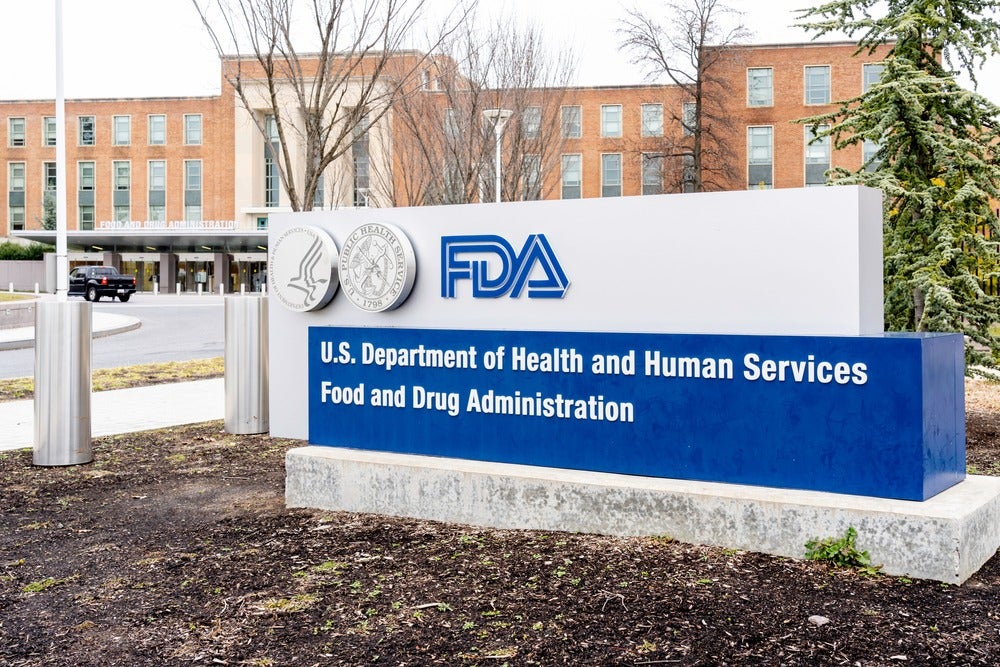
The issue of regulation also makes flexibility an issue for OEMs. Once a product has been cleared by the appropriate regulatory body, the manufacturing processes and supply chains involved in mass producing it are still subject to these regulations.
The upshot of this is that if, for example, a company supplying the outer ring part for an implantable, artificial heart valve decides to change the type of machinery it uses to make this component, or moves its production facility to a new location, it has to send a change notification to the manufacturer of the final valve.
And, in turn, the manufacturer itself may then have to take measures to ensure there are no risks associated with this change of affairs – possibly by demonstrating equivalence to the previous setup, and informing the regulatory body that initially approved the device.
As Clarke says, “this makes it very difficult to move, or make certain changes, once you are already in the supply chain”.
The impact of localised disasters
A global pandemic is one thing, but environmental supply chain disruptors are something OEMs have had to contend with for many decades.
These predicaments typically come in the form of natural disasters and other extreme weather events – which can devastate entire cities, if not countries, but are often very hard to foresee ahead of time as well.
Previous examples range from the major wildfires that struck the US West Coast in the middle of last year, to the earthquake and resulting tsunami that devastated Japan in 2011, and the global disruption caused by the Icelandic volcano, Eyjafjallajökull, erupting in 2010.
Clarke highlights one even more recent instance of extreme weather negatively impacting medical device supply chains – the ice-cold conditions and record low temperatures, dubbed the “big freeze”, that are currently hitting parts of Texas.
“Many chemical companies in the state are having to write to all of their customers and tell them they may not be able to supply certain materials for the next, say, four-to-six weeks,” Clarke adds.
“That has a massive ripple effect throughout the supply chain as everyone starts to look for existing inventory – either from the same company or from distributors.
“This causes prices to rise, it could cause stockouts – and it might only be the supply of a very small component that jeopardises production of an entire medical device.”
And, because the medical device in question has received regulatory clearance to be made using a specific material from a particular supplier, it becomes extremely difficult for OEMs to adjust their supply chains in instances like this, and react to the situation in real time, while also conforming to the same regulations.
This, Clarke says, is where things like scenario planning and risk analysis come into play – and are critical for multinational medical device firms and industry SMEs (small and medium-sized enterprises) alike.
Scenario planning: What can companies do to mitigate these risks?
If single sourcing materials and components from one supplier is, as Clarke describes it, “putting all your eggs in the same basket”, then it’s easy to see why the concept of dual sourcing has become more widely embraced by the medical device industry.
Dual sourcing involves splitting supply of the same parts between two distinct vendors – and is arguably the most well-established method for mitigating against potential supply chain risks.
As well as the obvious benefit of providing a backup if one of these sources has to halt or slow its activities, dual sourcing also offers scalability.
This is because, if there’s a sudden increase in orders, an OEM can switch to another supplier for a short period of time rather than expecting a single supplier to ramp up production overnight.
Another method Clarke highlights is multi-site sourcing – something he believes offers additional advantages compared to dual sourcing.
Multi-site sourcing refers to the process of a manufacturer sourcing its materials and components from more than one site run by the same supplier, circumventing the issues that may arise if one supply chain goes down, but with the added convenience – and possible cost savings – of only having to deal with a single vendor.
“It’s a more cost-effective, value-driven backup plan compared to dual sourcing, because you get the best of both worlds,” Clarke says.
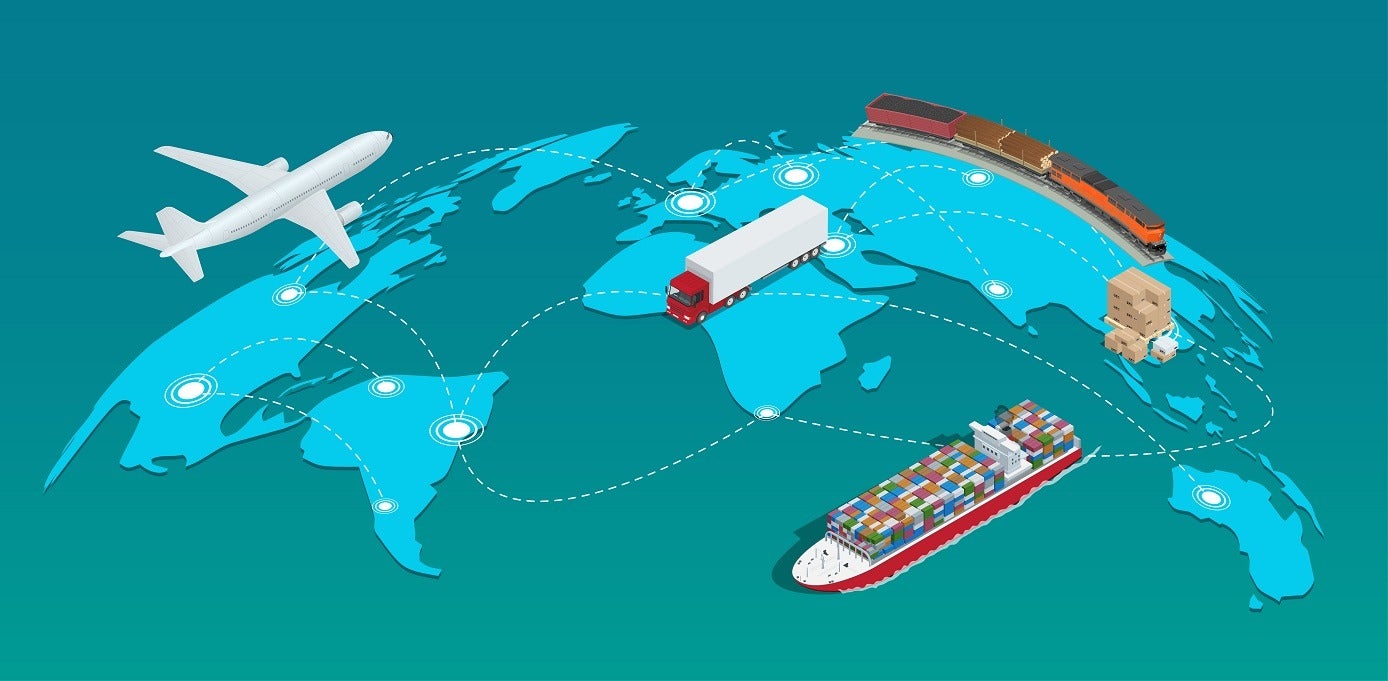
“You can leverage a certain supply volume with one particular vendor, but you still have that contingency built in through having multiple sites in different areas.”
As an established, multimillion-dollar provider of plastic and rubber polymers, Tekni-Plex itself has the capacity to offer this kind of setup to OEMs through multiple extrusion facilities in a diverse range of locations – including three in the US, one in Europe in the Belgian city of Aalst, and another in China.
Another capability that larger, more experienced suppliers like Tekni-Plex, 3M and Evonik can offer manufacturers is something Clarke dubs “vertical integration”.
This goes a step further by involving the supplier, to an extent, in the manufacturing process, and potentially creating “mega vendors” that can do a lot more for their customers.
It may refer to a supplier undertaking small subassemblies of multiple components, or adding certain features to an individual part before it reaches the manufacturer of the final device – for example, a plastics specialist like Tekni-Plex could offer to insert a hole, or a chamfer, into a catheter.
Due to its utilisation of a single vendor, vertical integration holds a similar list of benefits to multi-site sourcing, with the main one being the fact it’s easier to manage one supplier rather than several.
However, it also brings a similar set of risks to multi-site sourcing as well, as a manufacturer will be faced with major supply chain disruption if that one vendor experiences a problem that affects the entirety of its production means.
The globalisation problem
The rise of the internet, improved international communication and generally more positive political relations have all played a part in globalisation growing exponentially over the past few decades.
And, while it’s widely accepted that this is a good thing for cultural diversity, trade, travel, innovation, technological advancement and the overall enrichment of society, globalisation is not without its drawbacks – a fact that has been highlighted in brutal fashion throughout the Covid-19 pandemic.
The most obvious and sustained impact is unquestionably the spread of the virus to every corner of the globe, with countries hosting larger tourism industries and international travel hubs affected worst of all.
However, the crippling disruption to supply chains everywhere is probably second only to this when discussing the part played by globalisation, and the interconnected nature of economies across the world, in the pandemic.
This has led many – Clarke included – to raise the issue of local supply sources versus global supply sources, and the pros and cons associated with each.
“The pandemic has definitely highlighted the disadvantages of globalisation to a certain extent, and people are now pushing more and more to have things locally,” he adds.
One notable impact is that the transportation of components has become more costly across the board, leading suppliers to raise prices – particularly for parts that are coming from overseas or travelling a great distance.
And, while some companies have chosen to try to weather the storm of these prices going up by continuing to import components from far and wide, others have started to realise it may be beneficial to source certain supplies locally and improve affordability, as well as their supply chain security, in the process.
“But, it depends on the materials and the components in question too,” says Clarke. “If it’s something bulky and heavy, it doesn’t make sense to ship it from halfway across the world, but then there are more specialised parts whereby it doesn’t really matter where you’re sourcing them from.
“So, local is important – but you do have to be scalable as well.
“And, if you’re making a global, high-volume device, you will want to have manufacturing in the key regions you sell to, as well as being approximate to the right suppliers in those places.”
As well as the fact that solely local supply sources do carry these limitations relating to scalability, especially for larger, expanding firms looking to branch out into new territories and become a truly global entity, another drawback is immediately apparent when returning to the issue of natural disasters.
Ultimately, if a region is hit by extreme weather, or an entire country is affected by a significant geopolitical event like new trade restrictions or an economic collapse, a device manufacturer getting all of its parts from local sources may well find these disruptions impacting every aspect of its supply.
Coping with a worldwide pandemic and planning for future crises
Many of the same scenario planning and risk mitigation measures mentioned earlier can still help during a disaster as far reaching as a global pandemic.
The way Covid-19 spread across the world last year meant it hit different places at different times. Originating in China, it affected the Asia-Pacific region first, followed by Europe and the US, and then South America and Africa – and, by the time the virus was reaching its peak in the Western world, some places in Asia were already moving to lift lockdown restrictions.
As Clarke points out, this created a unique challenge regarding global supply chains, because manufacturing was down in different territories at different times – meaning backup suppliers established through dual or multi-site sourcing in one country could still help to offset the impact of suppliers having to shut down in another.
Alongside these practical and logistical issues, however, is the human element of a devastating global pandemic that has affected everyone’s lives so profoundly, and continues to do so.
Struggles with mental health, the fear – and, sometimes, tragic reality – of losing loved ones, adjusting to working from home and isolation have all contributed to a “huge emotional toll” that so many have been burdened with throughout the crisis, according to Clarke.
These factors have led many workforces to be far less productive overall, and are only compounded by staff having to take time off following a positive Covid-19 test – or, even worse, entire manufacturing facilities being forced to close temporarily due to a viral outbreak.
A lot of these difficulties are not something companies would necessarily have to reckon with following a more precedented crisis like an extreme weather event. On the flip side of this, however, there is the more positive human element of the pandemic, which has seen companies collaborate like never before and build cross-industry bridges to overcome this plight.
“One good thing that we did see in response to Covid-19 was that, particularly in the first few weeks of lockdown last year, I spent a lot of time taking phone calls from competitors, from people in hospitals, and from all sorts of companies who had this Utopian idea of trying to help wherever they could,” says Clarke.
“And, what you will see – even now – is that, when there’s a shortage of equipment, people will prioritise PPE, or ventilators, or other therapies used in the fight against Covid-19.
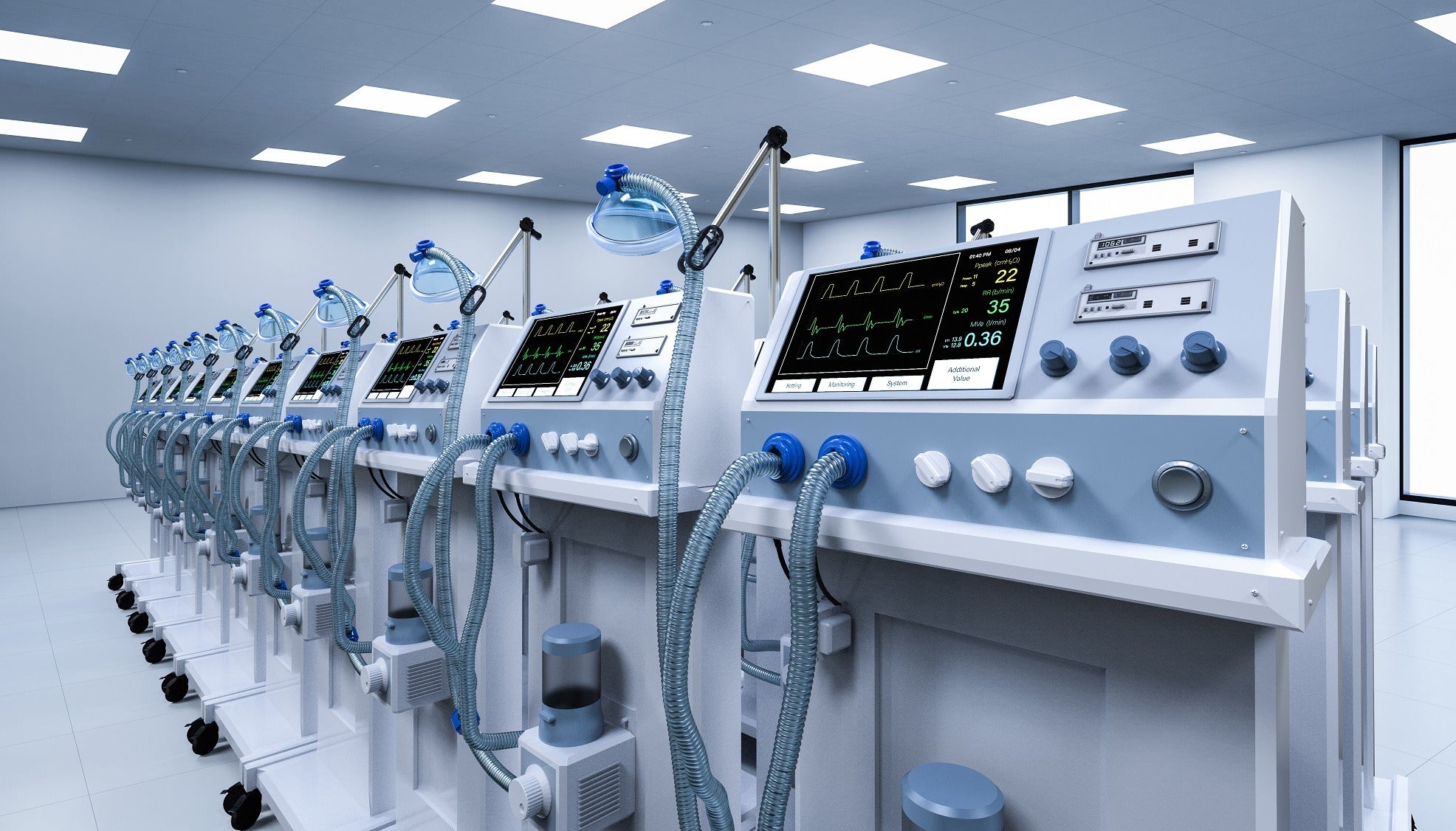
“It’s also very, very likely that people in the supply chain, even those that are competing for these finite resources, will accept that as well.
“I don’t know how long that will continue for – at some stage we are going to go back to trying to knock each other off due to the competitive element – but it was very nice to see on the human side of things.”
Ultimately, there is a limit to what OEMs can do to prepare their supply chains for something as widespread and inescapable as a pandemic global.
Companies – especially smaller firms with limited resources – can only build in so many fail-safes, and, as Clarke points out, it becomes an issue of what constitutes a reasonable investment into scenario planning at a certain point as well.
But, while even the most financially stable, market-leading manufacturers may not be able to account for all eventualities, Covid-19 has unquestionably highlighted many existing supply chain gaps with the potential to damage medical device production in the event of future disasters.
“If there’s one overriding lesson to be learned from the pandemic, it’s that you have to expect the unexpected – and plan for just in case, rather than just in time,” Clarke says.
“For manufacturers, that means looking at your supply chain in its totality, and doing your due diligence on your suppliers.
“Have they got backup plans? What are their disaster recovery plans? Do they have different sites and facilities? How far will your materials have to travel?
“All these things – along with striking a balance between local supply and global supply – are going to be the real lasting legacy from the pandemic.”