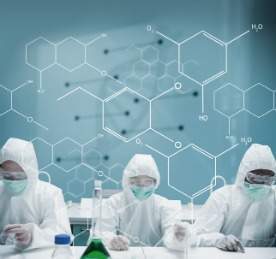
It is fair to say that, prior to going into hospital for an operation or medical procedure, the effectiveness of the lubricious coating on the medical device(s) involved is unlikely to pass through a patient’s mind. But, if such an intervention were to go ahead without this effective lubricious coating, they would certainly feel it when they came round afterwards, as Dr Clement Higginbotham, director of the Materials Research Institute at the Republic of Ireland’s Athlone Institute of Technology, makes clear.
"A key priority when it comes to lubricious coatings is wettability, because the more you can minimise tissue damage and patient trauma, the better," Higginbotham explains. "Plus, the greater the wettability, the more likelihood you have of reducing the need for extra procedures.
"It is about achieving a balance. The lubricious coating needs to be non-slippery when it is in the physician’s hand, but when it meets the aqueous environment inside the patient, it needs to become slippery as quickly as possible," he adds.
Wettable, lubricious hydrophilic and hydrophobic coatings have been around since the 1970s, and are arguably one of the key – yet unsung – medical device innovations of the past 40 years. Moreover, they are an integral element of one of the most rapidly expanding areas of the medical devices market, namely minimally invasive devices.
It stands to reason that insertable devices, such as catheters or guidewires, need to present as low-friction a surface as possible once inserted and exposed to blood and other body fluids, in order to reduce or prevent inflammation or injury, help to prevent infection, and minimise patient discomfort.
From the early days of lubricants, such as glycerine, silicone oil and even olive oil, technology has advanced swiftly, but the priority remains much the same – lubricity and durability, argues Higginbotham. Lubricious coatings will normally be water or solvent based and, in order to activate the chemical reactions, heat, UV, plasma or corona will normally be applied.
"The vast majority of lubricious coatings are on catheters, and they are most prevalent within the cardiovascular and urinary arenas," says Higginbotham.
Ophthalmology is another area where such coatings have proven extremely beneficial – in the delivery of intraocular lenses, for example, as the delivery cartridges used to place the lenses must employ slippery surfaces to reduce damage. Such coatings can also be beneficial in diagnostic devices, such as glucose meters, which may require a coated film component to ensure the liquid sample spreads evenly before it is inserted into a reader.
Lubricious coating selection
Device designers have a variety of synthetic and naturally derived coating systems to choose from when it comes to lubricious coatings, as well as different ways to bind them to the target substrate. Therefore, it stands to reason that the device material and type of additives used will be important considerations – as there can be a knock-on effect on coating adhesion and durability – and may be the difference between a hydrophilic coating adhering tightly or not at all.
Issues such as the coating’s antithrombogenicity, as well as its resistance to bacterial and protein attachment, are factors that need to be considered. Various combinations may also need to be tested, especially if the chemical interactions between the coating and drugs are not constant.
"Biocompatibility is an important consideration when looking to select the right lubricious coating. You need to try to start with polymers or monomers that you know are reasonably non-toxic," continues Higginbotham. "Ideally, you’d want them to be actively biocompatible – a biomaterial that takes an active part within the body in attaching cells, for example. Alternatively, it just needs to be inert."
The thickness of the coating is another important consideration. "There is a big focus among researchers on trying to develop thinner and thinner coatings, with monolayer coatings being the ultimate goal," says Higginbotham. "In fact, we may not be far off achieving monolayer coatings, as it is not that difficult to lay down mono layers.
"The ease of hydration is another significant factor to consider; how hydrophobic is it going to be, and how quickly is it going to take in water? How durable is it going to be is a vital consideration, and something that may require a lot of field testing; how easily, for example, does it come off if it is rubbed – that is, how does it react to friction testing?
"Other issues include the sterilisation of the coating: what is going to be the best way to sterilise it; how susceptible will it be to radiation damage? Ideally, you want to know this before you develop the coating, but often you will only be in a position to know this when it is on the device. A further consideration is also the substrate being used," explains Higginbotham.
Shaping the next generation of medical devices
"One of the big challenges for the future is the durability of the coating; there is a lot of research going on in this area, trying to improve durability and the speed at which a coating is able to hydrate," Higginbotham continues. "There is also a lot of focus on developing multifunctional coatings, so we will have a coating that is not just able to deal with infection, but is also able to be used
to deliver different drugs.
"Another interesting area for the future is the development of multifunctional coatings that can release several different drugs, which will do different things or release at different rates," he continues.
"So, you might be able to combine anti-inflammatory, antimicrobial and anti-infection properties into the same coating, which will help immensely in the treatment of the patient. You would also be able to target drugs at a particular area much more effectively.
"Nano coatings are also an area that is potentially exciting," he concludes. "There will be a nano layer or nano particles through which we can create stronger bonds between the substrate and the coating. There is a lot of work going on in this area."