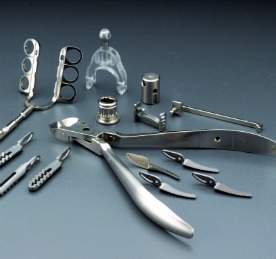
In terms of global manufacturing, present day technological needs are being examined both from a cost standpoint as well as with regards to added value. Every medical device manufacturer is looking at the possibility of having a leaner supply chain without sacrificing qualitative needs.
Biocompatible materials have in recent years really begun to shape the development of medical devices and expand the potential for developers and manufacturers as well as, ultimately, the treatments offered to patients. However, they have posed challenges for manufacturers as their contours and shapes can be complex. Metal injection moulding (MIM) is a manufacturing process that has helped many global medical device manufacturers to meet those challenges.
The MIM process arms medical device makers with the ability to design unique products without the cost restrictions associated with conventional metal-forming techniques. Medical device manufacturers are impressed with the freedom MIM offers. It suits their needs and allows them to focus on identifying new-generation technology that can help provide cost-effective solutions, while keeping quality and safety requirements intact. The MIM process combines the design flexibility of plastic injection moulding with the strength and integrity of wrought metals. MIM technology has proven itself to be a viable method for the production of complicated and complex-shaped contours of metal components used in diverse applications such as endoscopic and laparoscopic instruments, orthodontic, and surgical tools, and implants. These are made from stainless steels, cobalt and titanium alloys, and ceramics. Surveys have also concluded that the MIM process is sustainable since it generates comparatively less CO2 and consumes less water.
The MIM process
The basis of MIM technology involves fine metal powders, which are combined with thermoplastic binders that allow them to be injection-moulded in a plastic injection moulding machine. Once moulded, the part is subjected to high temperatures in a controlled atmosphere where the binder burns away and the metal particles fuse into a near fully dense solid. Similar to plastic injection moulding, MIM part geometry has few limitations, which makes it very inexpensive to mass-produce highly complex parts once a tool is constructed. Metal alloy selections are virtually limitless.
Developed more than 25 years ago, the MIM process found its first medical applications in orthodontic brackets. These tiny complex shapes were ideal for the process and today MIM is the preferred manufacturing method. The explosion in laparoscopic surgical procedures in the past ten years has further driven the use of MIM in medical applications. Small and finely detailed parts such as endoscopic graspers are now economically made via MIM.
Confidence in the MIM process and materials has grown in the surgical instrument and implant manufacturing community. New applications for instruments, reusable tools to assist in surgical procedures as well as implants are now becoming a reality with cost savings and design flexibility being key drivers in MIM process adoption.
MIM parts are used widely in the following medical application areas:
- minimally invasive surgery (MIS): laparoscopic and endoscopic jaws, graspers, scissors
- general surgical: scalpel handles, nippers, forceps and instrument mechanism parts
- orthopaedic surgery: trauma plates, screws, spine (implants and external fixation) and orthopaedic surgery tools (power and hand type)
- open heart surgery: stabilisers and positioners and various other parts
- orthodontic and dental: orthodontic brackets, dental instruments and implants
- hearing aids: metal hook, tube element and various other parts.
MIM can manufacture most of the medical alloys offered by either the wrought or cast routes. MIM offers a wide variety of materials for medical applications such as stainless steel (300, 400 series, precipitation-hardened grades) and its nickel-free grades, Co-Cr alloys, and titanium and its alloys.
For instruments that require high strength and wear combined with good corrosion resistance, solutions can be found in MIM SS 17-4 PH, 420 and SS 440C-grade stainless steels. MIM 316L-grade stainless steel is a popular choice for applications that require high ductility and excellent corrosion properties. MIM nickel-free stainless grades are used for orthodontic applications.
Orthopaedic implant applications are growing for MIM, and the Co-Cr as well as titanium alloys with HIP processing are used for these critical applications. Parts can be fabricated out of difficult-to-melt alloys such as tungsten-heavy solutions. Any tailor-made chemistry can be formulated by MIM.
MIM materials have advantages such as homogeneous microstructure and isotropic material properties with no interconnected porosity. Hence, MIM is the most suitable manufacturing process for complex medical parts, with part performance and material properties on a par with the wrought and cast route.
Spinal surgery application
The various parts of orthopaedic surgery instruments, such as trauma plates, blades, screws, spine (implants and external fixation) and orthopaedic surgery tools (power and hand), are successfully manufactured by the MIM process.
The critical requirement of orthopaedic surgery equipment parts are: complex geometry; high length to thickness ratio; good dimensional consistency and close tolerances for proper assembly and function; material with high hardness and good corrosion resistance; and clean manufacturing process to meet the specified cleanliness in the final component.
One recent application developed for MIM is a retractor blade and ring set used in a spinal surgery procedure. Manufactured by Indo-MIM for a leading orthopaedic implant manufacturer, MIM resulted in a dramatic reduction in manufacturing costs without sacrificing product quality or function. Made in three lengths, the retractor blades offer the surgeon easy access in order to insert the fixation rod during the procedure.
Previously made from wrought 17-4PH stainless steel bar stock, both parts required extensive multi-axis CNC machining as well as wire electrical discharge machining (EDM) to achieve the intricate detail. Indo-MIM was able to produce the products with its MIM technology in the 17-4 PH alloy and achieve the required mechanical properties and biocompatibility requirements. Indo-MIM’s cost-effective tooling and product development resources were able to tool up the three blade lengths and ring quickly, while still being economically viable for small-series production volumes.
MIS instruments
MIS has been widely adopted for certain surgical procedures and manufacturers are looking to design new devices that will allow open surgeries to be converted to minimally invasive procedures. MIS devices are highly complex, yet they need to be cost-effective in low to moderate production volumes. The following should be noted:
Laparoscopy and catheters are popular MIS procedures. MIS is expected to further reduce invasion and be used for microscopic operations in narrow spaces.
- Laparoscopic jaws and graspers for MIS instruments are successfully produced by metal injection moulding.
- Laparoscopic jaws, endoscopic jaws, graspers, scissors and instrument bodies for MIS have been widely manufactured by MIM.
- Tight tolerances are necessary for proper fit, form and function for the mating parts in the final assembly, and material with high hardness and good corrosion resistance is required for these applications.
- The clean manufacturing process to meet the specific cleanliness level in the final component is must.
- Indo-MIM produced the products with its MIM technology in the 17-4 PH alloy, and achieved the required mechanical properties and biocompatibility requirements at a significant saving.
- MIM has incorporated all of the critical features and geometry of
the parts in the injection mould,
avoided the machining, and produced the net-shape components.
Fixation plates
Another potential MIM candidate is the family of plates used in the plating system for the treatment of fracture fixation, reconstruction or arthrodesis of small bones, including those in the forefoot, midfoot and hindfoot. The characteristics of the plate call for a profile that allows fixation in various profiles as per a contour customised to specific anatomy to facilitate fusion or fracture reduction, and stabilisation. As the plate is compressed to bone, the plate will further contour to the specific anatomy of the patient.
Many of the plates also incorporate a slot used to assist this compression and they need to have a matching profile to house the head of the special screws. MIM meets the challenge of biocompatibility as well as complexity owing to its unique capabilities. It manages to meet the low-volume, high-variety requirement of such an application, thereby allowing the surgeon to offer problem-free treatment.
MIM has been used as a successful manufacturing process for complex parts for various medical products, meeting high quality and regulatory requirements with a variety of medical materials.