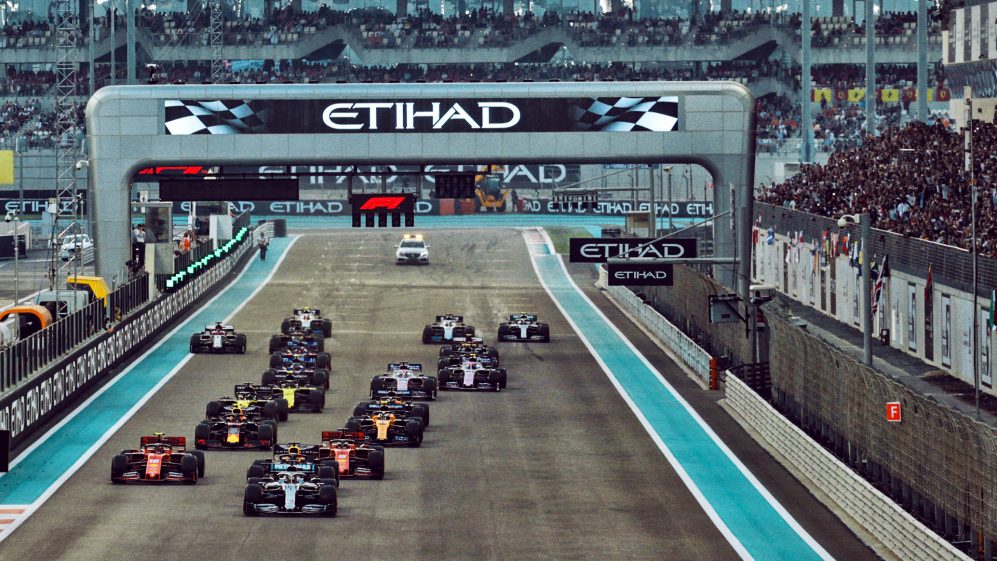
The Covid-19 pandemic has highlighted some glaring equipment holes in the global healthcare industry — most notably in the supply of ventilators, where manufacturing needs to raise productivity by between 500% and 1,000% to meet demand. Thomas Parker finds out how a wave of companies from outside the medical industry are helping traditional medical device makers to plug this gap in the UK.
The world of Formula 1 is typically fraught with secrecy, with some of the world’s brightest and best engineers working day and night to gain the tiniest of margins over their competitors.
And with each team’s cars constantly evolving over the course of a season, speed is absolutely critical.
“One of F1 race engineers’ great abilities is to design and test stuff extremely quickly,” explains Martin Passmore, professor of automotive aerodynamics at Loughborough University.
“They’ve been using equipment such as 3D printing to develop parts for a long time.
“This means you can design a component, build it for your wind tunnel testing work, and you can be testing it the next day, and then do another design.
“This ability to turn stuff around really fast is crucial for them.”
Right now, it’s a talent that could have a far wider impact than engineering the best race cars on the planet.
With the F1 season postponed until further notice, like most sports across the world, the vast workforces of UK-based teams have been redeployed to help build ventilators in super-quick time as part of the country’s response to the Covid-19 pandemic.
When the government issued a call for non-medical manufacturers to help plug a 20,000-plus gap in the number of breathing aid devices it needed to deal with the worst of coronavirus, the likes of McLaren, Mercedes, Ferrari, Williams and Red Bull stepped up.
How Williams Advanced Engineering is helping UK ventilator effort
Stuart Olden, a senior commercial and business development manager at Williams Advanced Engineering, is heading up the ventilator project for the technology and engineering arm of the Williams F1 team’s parent company.
Working closely with Smiths Group, one of the UK’s few ventilator producers, Williams has taken its partner’s 2D drawings for existing respiratory devices – which already have regulatory approval – and converted them into 3D geometries using its computer-aided design (CAD) systems.
This helps to speed up the process in engaging with the supply chain to source the required components and build prototype assembly processes that will mirror those used by Smiths.
“We’ve now moved into the next phase where we’re helping with tooling and test equipment engineering to support the assembly lines that are going to be set up to manufacture the ventilators,” says Olden.
“It’s a system our design engineers are very used to looking at, in terms of taking 2D PDF images of a part or component assembly, and then converting that into a CAD.
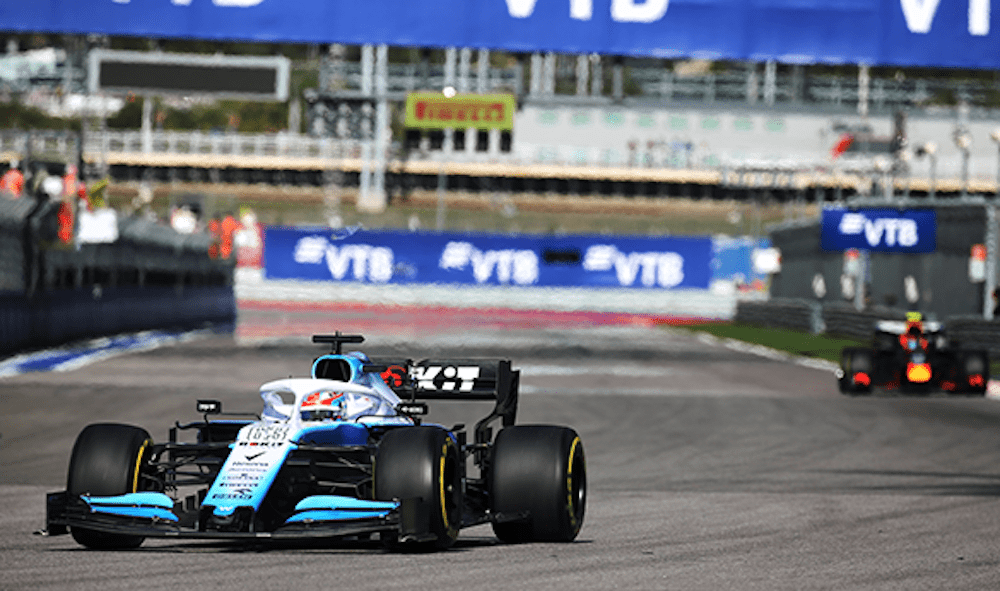
“We’re not changing anything from Smiths’ design – all we’re doing is helping to ramp up production quickly for the procurement of additional ventilators.
“In order to do that, the quickest way is to generate that 3D model to get out to the supply chain as soon as possible.”
Like many people in lockdown Britain right now, Olden’s team is mainly working from home – with only a handful of staff at the company’s base in Grove, Oxfordshire.
He adds: “I’ve had a team of about 35 to 40 design engineers working on the prototype and the 3D CAD models from their living rooms, studies, kitchens, dining room tables – wherever.
“And that’s all being fed into a central repository that we enable configuration control through, and then we’d pass that on to a single point of contact in the procurement team who puts it into their supply chain system.
“It’s a pretty proven model that we do on a regular basis. Obviously there’s some communication challenges when we’re all disparate across the south of England, but it’s been working really well.”
How industries are coming together to build ventilators
Williams Advanced Engineering and its F1 rivals are just part of a growing ecosystem of manufacturers from outside the medical devices world that have lent their services in a national effort that has been likened to during the Second World War – when car companies including Ford, Vauxhall and Rover repurposed manufacturing to build military aircraft, tanks and weapons for the Allied forces.
It was on 15 March – eight days before the country was placed on lockdown – when the UK government said it was looking for businesses that could support in the supply of ventilators and ventilator components as part of its response to Covid-19.
Breathing aids are a crucial part of the care process for patients severely ill after being infected with the coronavirus, occasionally during transportation to hospital by ambulance and often while in intensive care units (ICUs).
The most basic types, known as non-invasive ventilation, involve a mask that can be fitted over a patient’s mouth and nose to help them breathe easier
Mechanical ventilators, on the other hand, feature a tube being inserted into the airway. It is connected to a machine that moves air in and out of the lungs when they have been taken over by the virus and make it a struggle for a patient to breathe.
These complex machines – which also feature digital controls for air pressure, and a humidifier to match air to body temperature and add moisture – offer the best chance of survival for these people most at risk.
An Imperial College London study in March estimated 30% of hospitalised Covid-19 patients could require mechanical ventilation.
At the time of the government’s announcement, the country had 5,000 adult and 900 child ventilators, but it was estimated the UK could need at least 30,000 in total to cope with Covid-19 when cases peaked in the country.
Downing Street labelled it a national priority and said it wanted the manufacturing sector “to come together to help the country”.
“We need to step up production of vital equipment such as ventilators so that we can all help the most vulnerable, and we need businesses to come to us and help in this national effort,” the government added.
Similar cries for help have been issued in the US and Italy as the global ventilator shortage hit 880,000 by late March, according to analytics company GlobalData.
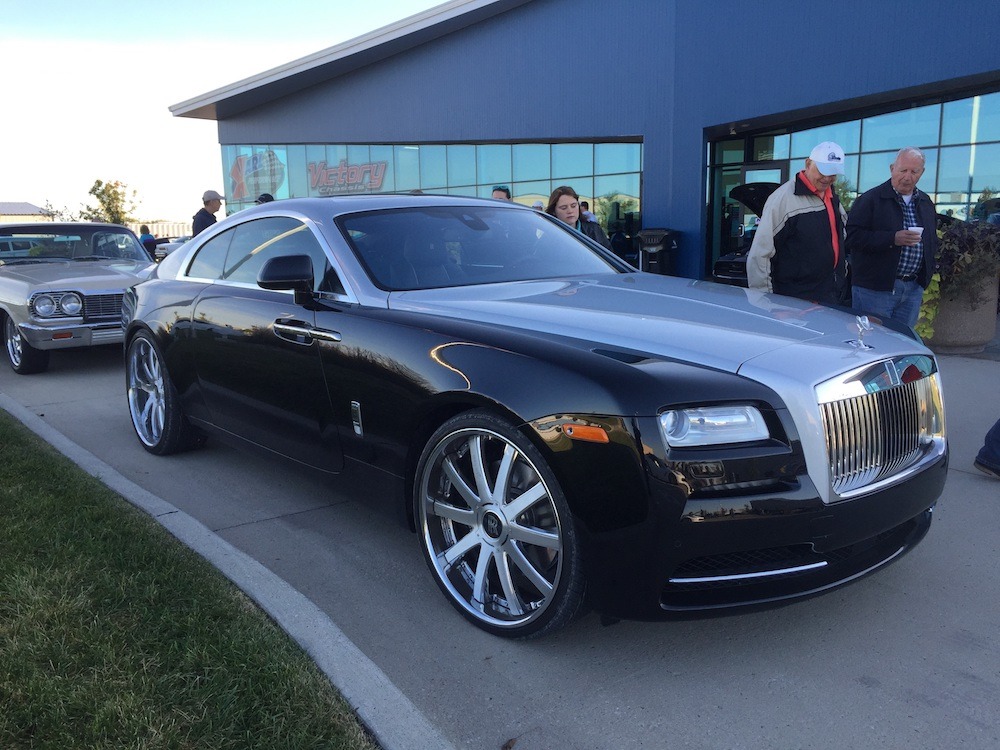
And just as companies including Ford, GE and Tesla have used heating, ventilation and air-conditioning factories to produce respirators in the US, the VentilatorChallengeUK consortium has been established in Britain.
Alongside seven UK-based F1 teams, there are firms as diverse as Rolls-Royce, Airbus, Accenture, Dell Technologies, Siemens and Unilever involved.
Run by High Value Manufacturing Catapult — which was set up by the government-led initiative Innovate UK to grow manufacturing in the UK — the organisation is using two existing ventilator designs to upscale production.
One of these is Smiths Group’s portable paraPAC plus, which Williams is helping to build.
The device, which is lightweight and portable, delivers oxygen to the lungs of sick patients to help them breathe, taking some of the strain of the lungs.
The firm says these can be used during emergencies, when a patient is being transported to and around medical facilities, or wherever they’re needed.
The London-based multinational engineering firm says it will increase its own production of this ventilator model, and is working to fulfil some 25,000 orders it has received from Italy and Germany.
It’s also in talks with contract manufacturers to increase capacity in the US and other countries to help meet global demand.
Under normal circumstances, a few dozen employees working one shift, five days a week, turn out between 100 and 200 units a week.
The company says this could increase to between 200 and 300 employees across three shifts for seven days, producing four-times the usual amount.
Smiths’ chairman Sir George Buckley says: “These are skilled workers who can be retrained. It is an assembly job for the most part and they can do it.”
The other ventilator being developed by the VentilatorChallengeUK consortium, and reportedly government clinicians’ first choice, is the ESO2 system developed by Oxfordshire-based firm Penlon.
A device typically used in ICUs, the new ventilators from its Abingdon plant rolled off the production line over the first weekend of April and were delivered to NHS hospitals the following week.
How Dyson is helping the UK ventilator effort – but doubts persist
Located in rural Wiltshire, RAF Hullavington has a rich wartime history of hosting top Allied officials, Bristol Blenheim bombers and Met Office planes during the 1940s.
It even held the World Aerobatic Championships in 1970, and is a designated conservation area by charity English Heritage, but since 2016 it has been owned by Dyson.
The technology company, which has its headquarters in the nearby town of Malmesbury, has established a global reputation as an innovator with its bagless vacuum cleaners and touchless hand dryers – and the decommissioned airfield was home to Dyson’s electric car project until it was moved to Singapore in 2018, before collapsing a year later having proved a touch over-ambitious.
Similar accusations have been pointed at the firm now as it repurposes the site to manufacture a new type of ventilator it designed in just 10 days, but founder and CEO Sir James Dyson remains confident in a project that runs parallel to the VentilatorChallengeUK scheme – whose sole purpose is to upscale production using established blueprints.
He says the UK government has ordered 10,000 of the devices, named CoVent, and promised to donate another 5,000 systems to the international relief effort.
Dyson is working alongside The Technology Partnership — a group of British scientists and engineers aiming to drive innovation — to build the bed-mounted and portable breathing aid.
It also operates on batteries, which means it can continue to be used in different care settings, including field hospitals and ambulances.
CoVent is powered by a Dyson digital motor, which has been re-engineered to meet the requirements of the ventilator and, the firm says, makes it particularly well-suited for industrial, high-volume production.
It’s also designed to achieve a high-quality air supply, drawing on its air purifier expertise.
Experts from the NHS, and Medicines and Healthcare products Regulatory Agency (MHRA), the UK’s medical devices regulator, were involved throughout the design process.
In a letter to staff, Sir James said: “This new device can be manufactured quickly, efficiently and at volume.
“The core challenge was how to design and deliver a new, sophisticated medical product in volume and in an extremely short space of time. The race is now on to get it into production.”
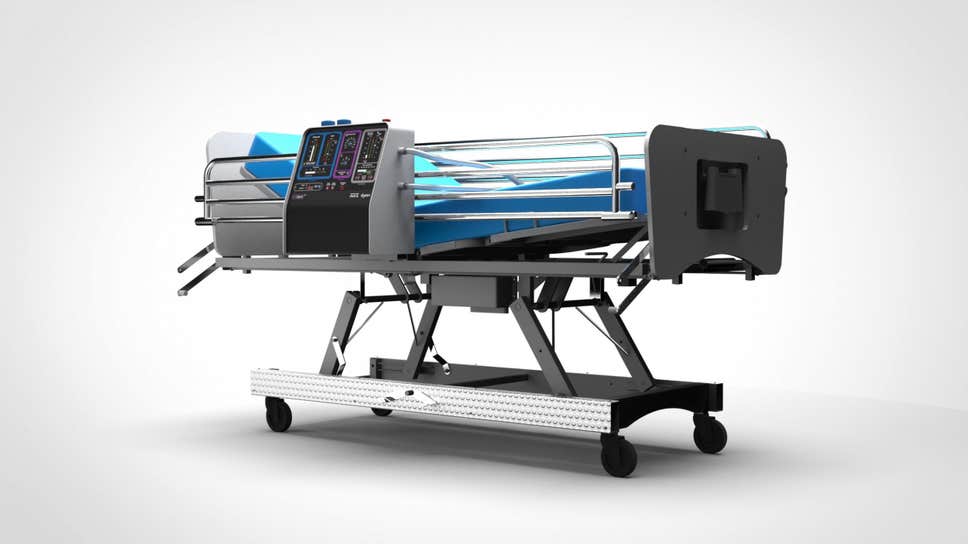
A Dyson spokesperson said the CoVent would be ready for use by early April but doubts have been raised about the possibility of making such rapid progress from ideation to production in an industry often characterised by conservatism and caution.
Speaking to the BBC just days before the VentilatorChallengeUK consortium was established, Penlon’s head of products Craig Thompson said: “The idea that an engineering company can quickly manufacture medical devices, and comply with the rules, is unrealistic because of the heavy burden of standards and regulations that need to be complied with.”
He added that “the focus should be on existing medical device companies increasing supply of ventilators”.
Prof Nick Oliver, from the University of Edinburgh’s Business School, also highlighted the need for “painstaking testing, refinement and a deep understanding of the context of use”, calling on policymakers to prioritise helping medical device experts to ramp up production rather than tasking other industries to develop new products.
“Celebrating inventiveness and resourcefulness is all well and good, but this is not the top priority at the moment,” he told the broadcaster.
For Nick Grey, founder and owner of Worcester-based vacuum developer Gtech, Dyson presents an obvious option in many ways – even though his own company was asked by a senior government official if it could help plug the ventilator shortage.
Recalling the initial conversation on a Sunday morning, he says: “I told him ‘I don’t know what a ventilator is really, but I’ll have a little look’, so he sent me over a couple of web links.
“And later that day, I was invited into an online call with around 20 or 30 people to discuss the proposals.”
Gtech’s proposal was eventually turned down but he bears no grudges, adding: “It’s a very sensible step because Dyson is used to making air-moving products, and it has much bigger facilities than Gtech.
“I’d said all along that I could build some, but I haven’t got the space. I’ve got a warehouse but I’d need to put benches and manufacturing equipment in it.
“So the government naturally and sensibly thought, ‘Gtech is the right sort of company but it’s not big enough, so there’s an obvious alternative’.
“Dyson has thousands of people, whereas we’re a team of five, so I think it’s a perfectly sensible decision to use its plans instead.”
Construction equipment firm JCB has reopened a factory that will make metal housing for Dyson’s ventilators.
A team of 50 engineers and manufacturing staff have been mobilised for the project and the company wants to build 1,000 casings per day.
JCB CEO Graeme McDonald told BBC News: “It’s very different to what we usually do but the basics are still the same.
“It’s still a piece of metal that needs to be capped, bent and painted, so it’s right up our street in that sense.
“All the team involved have done a fantastic job to do what usually takes weeks and months in a matter of days.
“It’s a real national effort. This isn’t an economic crisis but a health crisis, and every company in the UK wants to do its part right now.”
How is a ventilator built?
Modern-day ventilators are based on technology that was developed during the Second World War to supply oxygen to fighter pilots flying at high altitude, before being adapted to hospital breathing aids in the 1950s.
Although new features have since been added – improving flow delivery and exhalation valves – the fundamental designs have yet to be seriously updated as the medical devices industry moves towards smaller, wearable products.
And while they were once built in a single plant, the second half of the 20th century experienced a major shift in manufacturing across many industries that sent much of the production overseas as more sub-contractors came on board.
Former FDA adviser Kim Trautman, now executive vice-president of medical devices at US-based public health standards company NSF International, says this has led to a complex supply chain that could make it difficult for many of the manufacturers working on plugging the current ventilator gap.
“From a manufacturability standpoint, there’s a lot of different aspects to a ventilator, such as the hardware and the physical shell of the device,” she explains.

“There’s also software embedded in some pretty sophisticated integrated circuit boards.
“And then there’s a whole other set of accessory aspects, such as the plastic tubing and the connections for the ventilator – all the way through to what is being used to monitor the patient.
“We’ve got several different technologies, and more and more is being contracted out to speciality manufacturing.”
Businesses focused specifically on aspects such as circuit boards, injection moulding and extruding plastic for tubing all have a big role to play.
With many of these based in Asia, where the Covid-19 pandemic started, the supply chain has been severely disrupted for assemblers in Europe and the US.
Trautman adds: “Even if the specialisation has been in the US or EU, when something like this happens you don’t have delivery running on schedule and it causes big problems for the manufacturers.”
Reverse engineering a key part of F1 teams’ ventilator drive
These supply chain issues are the complications Dyson has sought to outwit by designing a “sophisticated” new system that’s suited to a “variety of clinical settings” and addresses the specific needs of Covid-19 patients, according to Sir James.
Another route could be via 3D printing some parts – a speciality for F1 teams that have been using the technology for a long time.
They can boast both additive manufacturing and CAD skills in abundance within their workforces.
Prof Passmore says: “They have a lot of machines for doing this kind of stuff in many different materials, and that’s an extraordinary advantage.
“It’s possible to print something that has components that are partly very stiff and partly flexible all in one go.
“Their ability to design something, make it and print it quickly is something they would be fantastic at.”
In order to better understand the two designs at the heart of the VentilatorChallengeUK project, F1 teams — alongside car developers — use a process called reverse engineering. Which involves taking apart pieces of equipment to find out how they were made.
“Car companies and F1 teams are pass masters at this stuff,” says Prof Passmore.
“F1 teams are not allowed to get hold of their competitors’ cars and dismantle them – that would be quite tricky.
“But of course, they’re all peeking and poking around, looking at other teams’ cars – particularly looking at any kind of aerodynamic devices on them – and saying ‘let’s go and build one of them and find out what it does’.
“The Japanese car industry started after using this method – copying the designs from European manufacturers by buying one, taking it apart and seeing how it’s made and what it’s made from.
“By taking stuff apart, engineers can tell what processes have been used in manufacturing different components, and they can find out what the materials are.”
Reverse engineering is being used by engineers at Mercedes-AMG, the six-time F1 constructors’ and drivers’ world championship-winning team, and scientists at University College London (UCL) to develop a continuous positive airway pressure (CPAP) breathing aid, which has been used in China and Italy to help Covid-19 patients.
A CPAP is a form of non-invasive mechanical ventilation, which applies mild air pressure on a continuous basis and keeps the airways continuously open in patients who are able to breathe on their own, but need help keeping their airway unobstructed.
These devices are already used in hospitals, but are in short supply and the research work at UCL’s engineering hub MechSpace could enable these to eventually be produced by the thousands.
Professor Rebecca Shipley, UCL’s Institute of Healthcare engineering director, told the BBC it took fewer than 100 hours between an initial meeting and beginning production.
“Normally medical device development would take years but we’ve done that in days because we went back to a simple existing device and ‘reverse engineered’ it in order to be able to produce them quickly and at scale,” she explains.
The partnership received regulatory approval by the MHRA, with the UK government ordering 10,000 devices — which are being produced “at a rate of up to 1,000 a day”, according to Mercedes.
The F1 team said 40 machines usually reserved for manufacturing F1 pistons and turbochargers are now being used to produce the breathing aids – while designs for its CPAP device would be made freely available to help fight the pandemic.
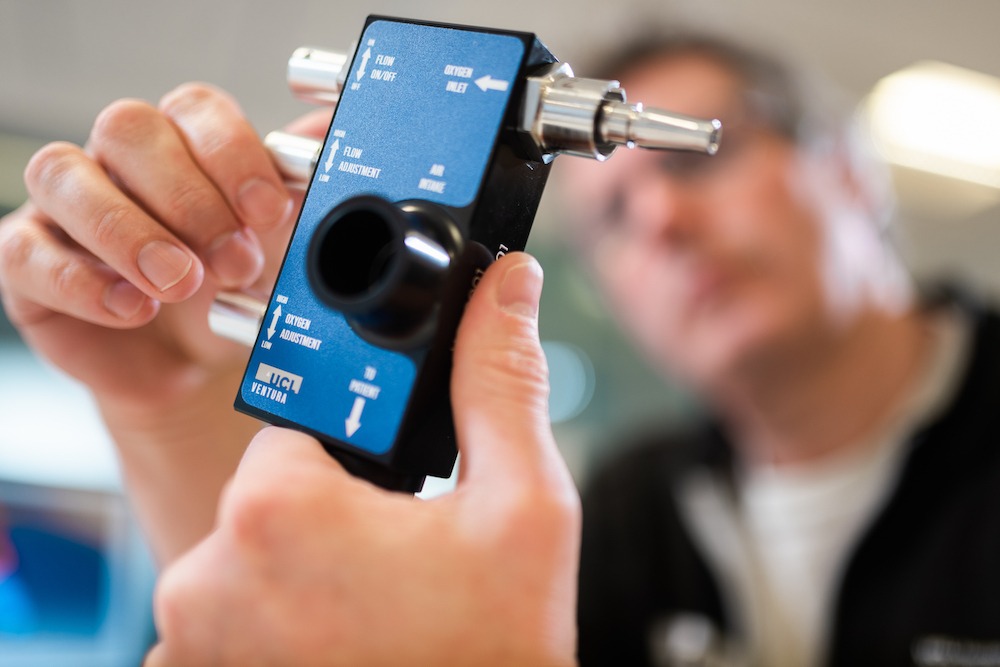
Speaking at the time of the announcement, Andy Cowell, managing director of Mercedes-AMG High Performance Powertrains — which is heading up the project — said: “Since the project was announced, we have received an incredible number of enquiries about the CPAP device from around the world.
“Making the design and manufacturing specifications openly available will allow companies around the world to produce these devices at speed and at scale to support the global response to Covid-19.”
Unlike F1 teams, the design cycle that many mainstream car manufacturers have is much slower due to the large amount of regulation involved in building a car for public roads.
The robust design processes that ensure everything going into a vehicle is fully validated and designed means timescales tend to be much longer.
But cut through the red tape and, once every nook and cranny on the assembly line is configured appropriately, the industry is hugely adept at producing incredible numbers of complex machinery in a short space of time.
It explains what the likes of Rolls-Royce – which made Merlin engines for the Spitfire and Lancaster bomber at its factory near Crewe during the Second World War – and Ford will bring to the table. With many car makers having ground vehicle production to a halt during the Covid-19 pandemic, it helps keep some workers in jobs, although the majority of companies in the UK’s combined effort aren’t taking profits.
Prof Passmore adds: “Car production lines are historically very bespoke, so an assembly line or parts of a production line are tooled up to do a very specific job. If you want to do something different, you would have to start again.
“I think there’s a lot more flexibility in more modern vehicle manufacturing lines, so robots can be reprogrammed to do something different. But having the experience of how to speed up manufacturing and production lines is something car manufacturers could come to very readily.”
How the government is streamlining its regulation to help new ventilator manufacturers
Standing in the way of any innovation in medical devices is a heavy set of regulations, overseen in Europe by national bodies like the UK’s MHRA but ultimately governed by the European Council, which set out new directives in 1993 to ensure high standards for health and safety. Nothing has changed since Brexit in January as Britain remains in a transition period.
The MHRA, formed in 2003, checks every part of the development phase of a product to ensure it’s safe for human use.
Derek Hill, professor of medical imaging science at University College London, explains: “When making a new design for a ventilator, you would typically start with a design you’ve already got and just improve it a bit.
“You might improve it by making it a little bit cheaper, or at a slightly higher spec so you can compete with your competitors.
“But the evolution of medical devices like ventilators is usually a slow and very controlled process.”
Yet, with the race well and truly on to fulfil the huge ventilator shortage as the number of coronavirus cases shoots up every week, manufacturing has needed to proceed much quicker.
Some companies may have to update their design, bringing in or developing new materials to build devices due to the difficulty in getting hold of the usual components.
But the likes of Dyson are also starting again from scratch and aim to get products on the production line within a matter of weeks, not the months and years usually associated with such innovation.
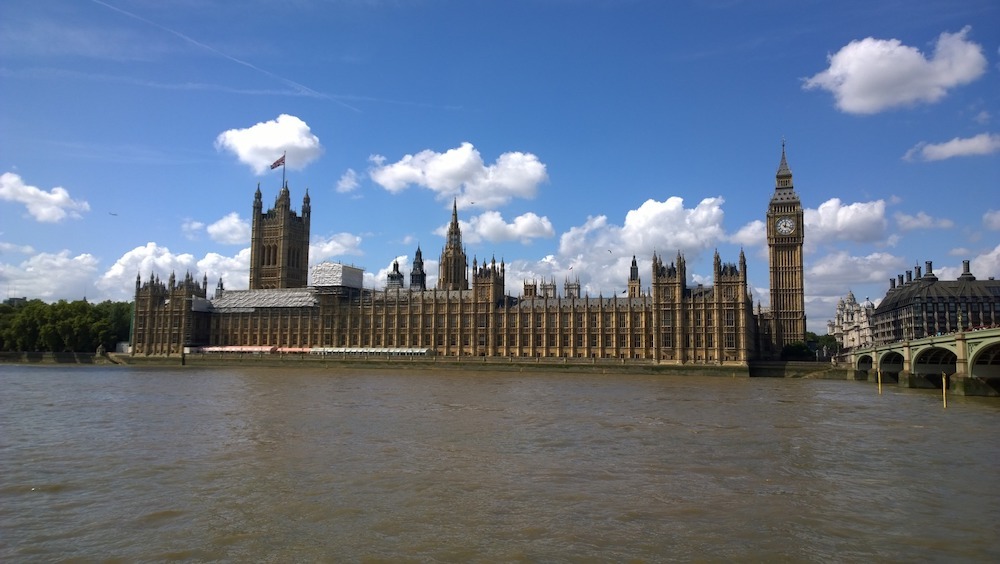
“There are rules about how you check and make sure any medical device, such as a ventilator, is designed and tested properly,” says Prof Hill.
“If you want to change the design of a ventilator there’s a whole load of checks you have to do, and normally all these things would take many months.
“For example, from starting a prototype of a new piece of electronics, which has the latest microcontrollers and embedded software, to having the first prototype could take about three or four months minimum.
“After this, it could take another three or four months to do all the technical documentation, and then after that you might be ready to go for formal regulatory approval.”
Manufacturers would have to go through similar testing processes if they change a single component on a device.
With a raft of industries outside medical devices lending a hand to develop ventilators, the government has derogated some of this red tape.
Derogation is a provision in EU regulations that allows for all or part of an assessment to be applied differently – or not at all when there is a public health emergency.
Prof Hill says: “That, in effect, means the government, which is issuing the derogation, takes on some of the risk from the manufacturer.
“Normally the manufacturer of a medical device is legally responsible and could be fined, sued by patients or its directors even thrown in prison if their company has been completely incompetent or dangerous.
“What you are doing with derogation is basically saying the government is taking over that responsibility, because otherwise an established company wouldn’t get involved and rush products out to meet the Covid-19 need.”
In order to adhere to the MHRA guidelines, businesses involved in the VentilatorChallengeUK scheme are strictly following the way the approved manufacturers develop and build their devices.
For example, to build the paraPAC plus ventilator, the assembly lines are using the same system Smiths Group uses to build the device.
Alongside this, the prototype produced by Williams was manufactured and tested at Smiths Group’s plant in Luton, which already has the necessary accreditation.
It’s partnerships like this that have brought together many industries previously alien to each other as they have responded to the government’s call to plug the ventilator gap.
Gtech’s founder Grey may no longer be involved but like many others, he’s proud to have played a part in some small way.
He adds: “We’re in this incredible period where, not since the Second World War, have British lives been affected by a global event like this to such an extent.
“And from my experience, almost everybody has stood up and said ‘if we can, we’ll help, tell us what you want us to do’.”