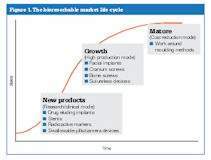
Micro-moulding in bioresorbable PLA and PGA materials creates challenges with small gate sizes for these highly shear and moisture-sensitive materials. This poses problems such as shear stress through small gates, humidity control for extremely small shot sizes, and integrating macro into micro-technologies to produce near micron-level geometry in precision, micro-moulded bioresorbable components.
As implantable and bioresorbable moulded parts approach micro or nano sizes, even a toothpick-sized runner is too large and too costly; bioresorbable raw material costs are between $3,000-22,000/lb. However, as the case study at the end of this article shows, micro-moulding with bioresorbable polymers can create an instant return on investment for moulding with net zero material losses in runner and sprue scrap.
Application of micro-moulding
Figure 1 shows common applications for bioresorbable micro-moulded components. In this life cycle curve, most of the work being done is in the new product area, R&D developments, drug-eluding products and implants being used as pharmaceutical carriers. Growth products in the hundreds of thousands of parts annually include bone screws, anchors and swallowable pills. Bone screws typically made of titanium can be replaced with bioresorbable materials so that patients are not ‘stuck’ with the bone screw for the rest of their lives.
Using the resorbable bone screw, after an approved amount of time, the bone fuses together and no longer requires the screw. The material then gets absorbed by the body, turns into carbon dioxide and water, and is flushed from the human system naturally.
The mature products segment is also very busy due to what is known as a workaround method, whereby conventional moulders may be putting micro-components into large mould frames and conventionally sized moulding machines. These programmes almost always provide an immediate return on investment due to the runners and sprues being so very costly in the material scrap they generate.
High-volume bioresorbable components require custom automation and metrology to handle, assemble and properly package for many temperature and humidity environments (two things bioresorbables cannot withstand well).
It is clear to our ‘tiny’ industry that the best way to handle a micro-part is to not handle it at all. If that mantra is upheld, how do we prepare the parts for assembly and how do we design in a ‘no handling’ process?
Part-handling of micro-moulding
Parts that are created and put down in a bin, bowl, guide or nest need to be picked up again, reoriented and reintroduced to the mating component or components next in line for the assembly. So each step that requires a part to be picked up and put back down adds error potential and, because they are micro-parts, there isn’t much room for error.
A few options exist, however, to avoid or at least minimise micro-part handling in a micro-assembly:
- create a micro-factory with tiny machines that enable one holding chuck or end-of-arm tool that interfaces with micro-mills, micro-moulders, or micro-stamping stations to create a micro-assembly line smaller than the size of a cereal box
- combine geometry in as few steps as possible (for example, valve/pump combinations, valve/chip combinations, micro-moulding, in-mould micro-assembly, six-axis micro-machining with indexing).
Micro-moulding environment
Let’s face it, we’ve all seen parts flick, stick, fly, fall, dive, tweak and bounce all over the place at one point in time. We’ve learned that valuable lesson of static elimination, the wonders of de-ionised air, and the criticality of temperature and humidity control in our environment. Under a polycarbonate transparent screen inside an automation cell, these conditions are heightened.
Laser welders, heat, parts riding on guides and metallic parts turning in vibratory bowls all create an environment not befitting micro-assembly. We must plan for static elimination and cleanliness to keep the dust from being disguised as our micro-assembly somewhere down the line. It is especially important for classified and certified cleanrooms to be installed via heap-filtration systems in micro-automation/assembly systems.
Micro-moulding part quality
As parts are assembled into sub-assemblies and final assemblies, the cost to scrap them escalates significantly. It is therefore important to consider the flowchart of an automated assembly cell that may require orienting parts to avoid gates, protrusions, wall thickness and anomalies.
The cost to scrap an assembly is much higher as each micro-part is added to the assembly automation system. For this reason, we identify and plan for parts’ anomalies and how, at each station, that anomaly will be positioned and properly oriented in the sub-assembly.
There are ways of determining what tolerances each part needs to have in order for its incremental or stack-up tolerances in the final assembly. This is called a tolerance study. A critical piece of the micro-device assembly and automation system, it is recommended that a detailed tolerance analysis is performed using ±6-sigma statistical tolerances such that a micro-assembly can be planned and executed with quantifiable and reasonable tolerances per part in the assembly.
There are several software packages that aid in this process but, as with any tool, it is important to understand the nuances in each micro-process that will feed the correct information into this study to get the desired and correct result.
Processing of micro-moulding
The first challenge encountered by processors of bioresorbables is material handling, which is the single-largest area for error. PLA/PGA materials are highly susceptible to moisture and heat. They must be stored properly (usually in a freezer) at a specified temperature in nitrogen-sealed foil pouches. They must then be used according to the processing run quantities needed and material drying cycle.
The material usage must be matched with the injection screw and shot size in an injection-moulding machine so that the material is not sitting in an improperly sized machine where over-drying and over-heating can occur due to the prolonged temperature and drying exposure.
Many material and processing platforms are used for bioresorbable assemblies. Each of these has nuances to consider in automated assembly.
Challenges of micro-moulding
Many challenges exist in micro-moulding but there are ways to minimise these challenges and the corresponding risk of failure to component manufacturers. These challenges include:
1. Modelling of micro-components
There remains a limited understanding of fundamental physics at the micro-scale, necessary to develop reliable models. Perfecting the mesh is critical to obtaining the correct result in any analysis. Because micro-parts have such small features (and therefore very large solid model sizes), a painstaking process in meshing a very high-resolution model is key to an accurate analysis.
2. Environment
Because a fraction of one single degree of temperature change can affect precision when machining or measuring at the sub-micron level, many micro-moulders and micro-machining experts enclose the entire machine and/or inspection area in order to create a controlled working environment.
3. Metrology and inspection
Inspection techniques in measuring very small micro-moulded parts require customised vises, tweezers and fixturing (not to mention extreme patience). Inspecting steel measurements usually provides a flat, robust surface that can be measured by non-contact means or in some cases contact measurement. The same surfaces that make moulded components can be used to ‘certify’ the dimensions much closer in repeatability and reproducibility than attempting the same corresponding measurement in micro-moulded components.
It’s not uncommon for the first article inspection to consume as much, if not more, time than the entire project combined. One of the latest time-saving techniques in this area, however, is laser scanning of the micro-part. This scans the part and turns it into a point cloud data. That data can then be directly compared with the nominal solid model to see visually where problem dimensions exist.
Only a select few sources of inspection equipment exist that are capable of measuring to sub-micron tolerances, and extremely clean and hepa-filtered, air-controlled rooms are necessary to the environment needed for repeatable measurements.
4. Part handling
Part handling can be challenging given the sizes of micro-moulded components. Many micro-moulders use edge-gated runners to carry their parts from one location to another and many are used as part of the automation process. If parts cannot be edge-gated, customised end-of-arm tooling, vacuum systems, reel-to-reel take-up equipment and blister packs are utilised accordingly.
Static electricity is a micro-moulder’s nightmare. Parts as small as dust can easily be lost if proper grounding of part collection systems, robotics, packaging and inspection systems are not performed. Static guns, wands, air curtains and grounding mats are commonplace in micro-moulding facilities.
5. Materials testing
In order to determine if the bioresorbable implant is robust enough, it is important to characterise the material during many different phases in the injection-moulding process. For example, PLA/PGA pellets in their raw form are stored in nitrogen-sealed pouches. Opening this pouch and exposing the polymer to a small degree of temperature and humidity starts to degrade the polymer immediately.
Consequently, PLA/PGA compounds must be dried in nitrogen-sealed hoppers in most cases and intrinsic viscosities must be validated throughout the injection-moulding process. Temperature from shear in the injection-moulding screw and barrel temperatures also decrease intrinsic viscosities.
Additional shear from small-mould gates are also a source of decreasing intrinsic viscosities. Once the PLA/PGA component is moulded, however, it has a protective skin around the moulded part and can be left for a small period of time outside of a nitrogen-sealed environment.
6. Validation
Due to the nature of bioresorbable polymers and their use in implantable devices, they are often processed in a classified cleanroom and validated using ISO 9001 and/or under ISO 13485 quality systems.
Throughout the moulding process, intrinsic viscosity values should be validated. Samples should be taken from the bag, after the drying process and after the moulding cycle by testing the runner and the part to compare shear effects through the gates, and after a period of time in the package, and through different temperatures for shelf life tests.
This testing will insure the validity of the implant throughout its life cycle in-vitro for form, fit and function of the implantable device.
7. Experiment design
By the time a 4.0 intrinsic viscosity material is processed, rapid deterioration of polymer properties can take place. If improperly processed, the material will act improperly in-vitro and cause an implant to resorb prematurely. There are tools available to test the impact of processing conditions on PLA/PGA materials. One of these is the gate shear test and tensile bar test.
The gate shear test has eight cavities with varying wall thickness from 0.05-0.23mm and the gate is always 75% of the wall thickness. The varying gates will simulate varying shear on the PLA/PGA materials. These ‘coupons’ are then tested for intrinsic viscosity loss and simulate what happens to a particular compound before an expensive shaped mould is built using
a similar gate size. The tensile bar, an ASTM standard for micro-moulding, can be used to test tensile properties of a given wall thickness.
Case study
Mature products in terms of cost and depreciation are seen when conventional injection-moulding methods are used to create moulded parts. This is typical when using 40-80t presses that require larger surface area moulds to fit in them. The material loss due to large paths in sprues and runners is extremely costly for $3,000/lb materials. These mature products always return on their initial investment to transfer to a micro-moulding sized mould and return even quicker with a runner-less mould.
Figure 2 shows a typical ROI for what is referred to as a ‘workaround’ conventional method to a micro-moulding method. A total of $4m in cost savings is realised when changing from a toothpick-sized runner and sprue to a runnerless bioresorbable mould. It would take just one moulding run to pay for the capital of micro-runnerless tooling/moulding machine. This is a controller’s dream and what is commonly referred to in the industry as a ‘no-brainer’.
Conclusion
There are critical steps required to handling, testing, processing, assembling and validating bioresorbable components. Material characterisation throughout the process is critical to understanding what happens to the intrinsic viscosity of bioresorbable polymers such that, when they are in the body, they will not prematurely resorb or stay too long for the implant to properly function.
As is usually the case in micro-moulding, this type of processing requires specialised equipment, design and validation expertise. Choosing the right supplier – one that is experienced in bioresorbable processing and microgeneration – will create a faster path to success.