Operating to ISO standards ensures that customers get consistent, high-quality products and services, which helps create a virtuous cycle for customers, patients, and suppliers
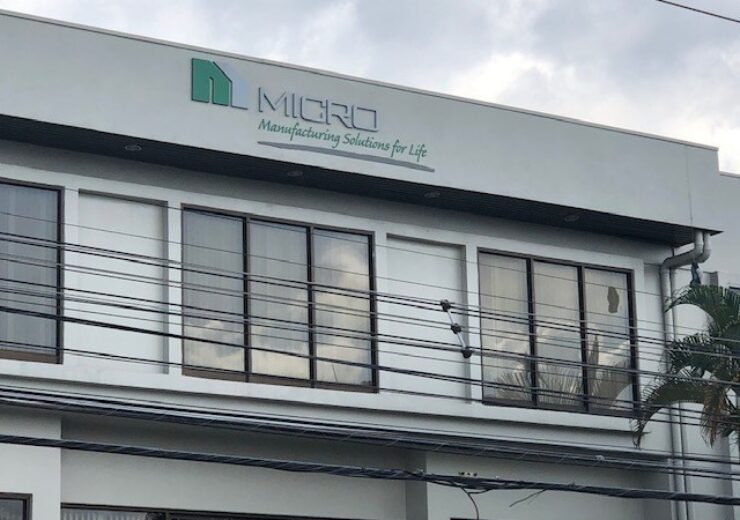
MICRO Costa Rica Office. (Credit: PR Newswire/ MICRO)
MICRO, a full-service contract manufacturing organization specializing in precision components, sub-assemblies, and complete devices for minimally invasive surgical procedures, today is proud to announce its Costa Rica facility has successfully implemented a Quality Management System in accordance with ISO 13485:2016. The facility is located in the Zona Franca Metro business park.
According to ISO (International Organization for Standardization), this standard is based on several quality management principles including a strong customer focus, the motivation and involvement of top management, a process-based approach, and continuous improvement. Operating to ISO standards ensures that customers get consistent, high-quality products and services, which helps create a virtuous cycle for customers, patients, and suppliers.
“This certification validates MICRO’s commitment to delivering the highest quality medical device products, which reduces risk for our customers and delivers optimal outcomes for patients,” said Brian Semcer, President, MICRO. “We are proud of the team effort put forth by our employees in New Jersey and Costa Rica which resulted in successfully completing the rigorous process to receive this critical certification. By implementing ISO 13485:2016, we can confidently manufacture to this exacting quality standard, which we believe is necessary when working in global markets.”
The Costa Rica facility opened late in 2021 including a new clean room assembly facility within the manufacturing center. This expansion, combined with three facilities in New Jersey and strategic sourcing partnerships worldwide, allows MICRO to provide ever-increasing capabilities and solutions to our customers through supply chain optimization and integration.
MICRO’s medical device division began 40 years ago developing ligation clips for use in surgical procedures and has grown to produce over 1 million endoscopic instruments annually in its environmentally controlled Class 8 clean room. MICRO’s Design for Manufacturability expertise allows us to help customers design components and assemblies that are optimized for production, keeping costs manageable and maximizing return on investment. MICRO continually invests in new technology, improved facilities, and employee training to take innovation to the next level and fulfill our Vision “To Help Our Customers Save Lives.”
Source: Company Press Release